Maximize Efficiency With These Wind Farm Remote Monitoring TipsMaximize Efficiency With These Wind Farm Remote Monitoring Tips
As wind energy continues to grow as a vital source of renewable power, wind farm operators face the challenge of maximizing turbine performance and efficiency. Implementing a comprehensive wireless remote monitoring system is critical for optimizing wind farm operations and profitability. Let’s explore why remote monitoring is so essential and how the latest technologies are transforming wind turbine management.
Real-Time Insights Optimize Turbine Operation
The ability to continuously monitor a wind turbine’s status provides operators with the data they need to identify issues early and take corrective action. Detailed performance metrics on factors like vibration, temperature, yaw alignment, and power output allows operators to fine-tune the turbine for peak efficiency. Subtle changes and anomalies can be detected before they lead to costly downtime and lost production.
For example, monitoring vibration through wireless sensors makes it possible to detect increased friction in the drivetrain before catastrophic failure occurs. Likewise, tracking temperature changes in the generator and lubrication oils can indicate developing problems long before an overhaul is needed.
Lower Costs Through Proactive Maintenance
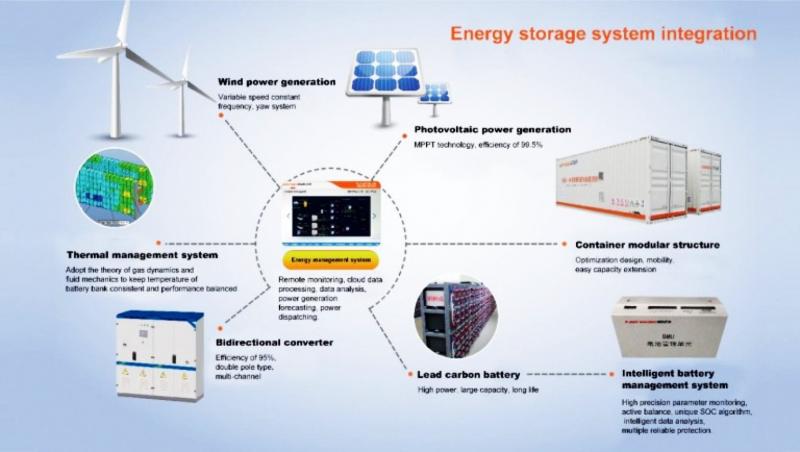
With round-the-clock remote monitoring, maintenance can be performed proactively when needed rather than on a fixed schedule. This condition-based approach reduces maintenance costs by avoiding unnecessary service calls. Operators can also troubleshoot issues remotely, often negating the need to send out technicians.
By catching failures early, damage to components is minimized. Small repairs can be made promptly before issues escalate or secondary damage occurs. With longer running times between major overhauls, the lifetime of capital equipment is extended.
Why Choose Wireless Sensors?
Traditionally, wind turbine monitoring required running expensive copper cables from each tower to the operations center. New wireless sensor networks offer a flexible and scalable alternative without the high infrastructure costs.
Self-contained sensors can be easily mounted on the tower, rotor, and generator to collect vibration, temperature, strain, and other data. This information can then be transmitted wirelessly to the central control room for monitoring and analysis.
Real-Time Data Enables Predictive Analytics
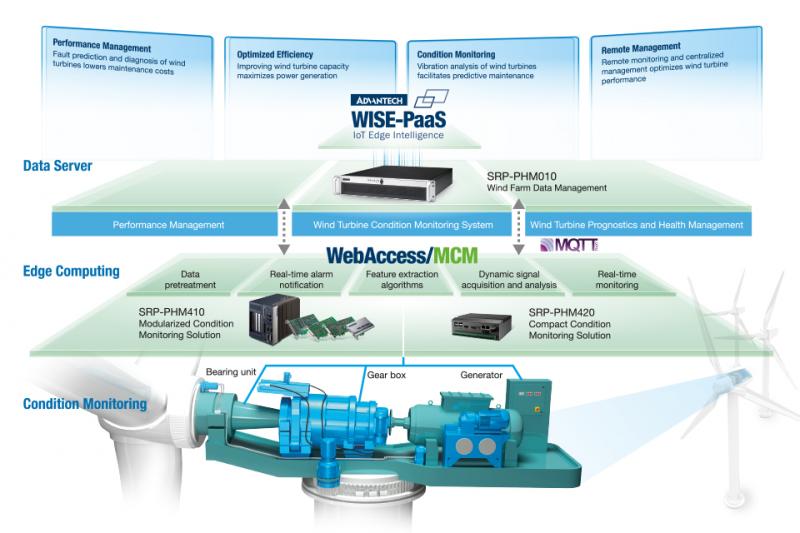
By compiling longitudinal data from each turbine, operators can utilize predictive analytics tools to detect subtle performance deviations and forecast maintenance needs. Machine learning algorithms can automatically identify patterns that indicate an impending failure or required service.
For instance, monitoring systems can learn a turbine’s normal power curve based on wind speeds. Any deviations from this curve would then trigger an alert, allowing operators to address the issue promptly.
The Future Is Automated
Ultimately, the future of wind turbine monitoring will be highly automated systems with self-diagnostics and AI capabilities. The goal is to enable turbines to automatically detect threats, diagnose their own operational issues, and even dispatch technicians when on-site work is required.
As monitoring technologies continue to advance, onboard controllers will integrate real-time data analytics directly into turbine control logic. This will allow turbines to autonomously optimize their performance while mitigating wear and tear.
Wind farm operators that leverage the latest wireless monitoring capabilities today will be well-positioned to capitalize on the automated systems of tomorrow.
When designing a wireless monitoring system, choosing the right sensors is crucial. The sensors will determine what types of data can be collected from the turbines, which directly impacts the actionable insights operators will gain.
Choosing the Right Wireless Sensors for Data Collection
Vibration Monitoring: Early Detection of Mechanical Issues
How does vibration monitoring contribute to turbine maintenance? Wireless sensors that measure vibration can detect increased friction in the drivetrain before catastrophic failure occurs. This early warning system allows operators to schedule maintenance proactively, preventing extensive damage and reducing repair costs.
Temperature Tracking: Predicting Component Health
Why is temperature monitoring crucial for wind turbines? Tracking temperature changes in critical components such as the generator and lubrication oils can indicate developing problems long before an overhaul is needed. This predictive approach to maintenance helps extend the lifespan of expensive equipment and minimizes unexpected failures.
Proactive Maintenance: Reducing Costs and Extending Equipment Life
Round-the-clock remote monitoring enables a shift from scheduled maintenance to a condition-based approach. This proactive strategy significantly reduces maintenance costs by avoiding unnecessary service calls and allowing operators to troubleshoot issues remotely. By addressing small repairs promptly, operators can prevent escalation and secondary damage, ultimately extending the lifetime of capital equipment.
The Cost-Saving Benefits of Remote Troubleshooting
How does remote troubleshooting impact operational costs? By diagnosing issues remotely, operators can often resolve problems without dispatching technicians to the site. This not only saves on travel expenses but also minimizes turbine downtime, resulting in improved overall efficiency and productivity.
Wireless Sensors: The Future of Wind Turbine Monitoring
Traditional wind turbine monitoring systems relied on expensive copper cables running from each tower to the operations center. However, modern wireless sensor networks offer a flexible and scalable alternative without the high infrastructure costs. These self-contained sensors can be easily mounted on various turbine components to collect critical data, which is then transmitted wirelessly to the central control room for monitoring and analysis.
Advantages of Wireless Sensor Networks
- Reduced installation costs
- Greater flexibility in sensor placement
- Easier maintenance and upgrades
- Scalability for expanding wind farms
- Improved data collection from hard-to-reach areas
Leveraging Predictive Analytics for Enhanced Performance
By compiling longitudinal data from each turbine, operators can utilize advanced predictive analytics tools to detect subtle performance deviations and forecast maintenance needs. Machine learning algorithms can automatically identify patterns that indicate impending failures or required service, allowing for proactive interventions.
Power Curve Analysis: A Key Performance Indicator
How can power curve analysis improve turbine efficiency? Monitoring systems can learn a turbine’s normal power curve based on wind speeds. Any deviations from this curve trigger alerts, enabling operators to address issues promptly and maintain optimal performance.
The Future of Wind Farm Monitoring: Automation and AI
The wind energy industry is moving towards highly automated monitoring systems with self-diagnostics and AI capabilities. These advanced systems aim to enable turbines to automatically detect threats, diagnose operational issues, and even dispatch technicians when on-site work is required. As monitoring technologies continue to evolve, onboard controllers will integrate real-time data analytics directly into turbine control logic, allowing for autonomous optimization of performance while mitigating wear and tear.
Benefits of AI-Driven Monitoring Systems
- Reduced human error in data interpretation
- Faster response times to potential issues
- Improved predictive maintenance accuracy
- Enhanced overall turbine efficiency
- Decreased operational costs
Selecting the Right Wireless Sensors for Effective Data Collection
Choosing appropriate wireless sensors is crucial when designing a monitoring system for wind turbines. The sensors determine the types of data that can be collected, directly impacting the actionable insights operators can gain. Several key factors must be considered when selecting wireless sensors for wind turbine monitoring:
- Data types needed (e.g., temperature, vibration, strain, humidity)
- Measurement accuracy and resolution
- Sensor operating conditions (temperature, moisture, vibration)
- Power requirements (battery or wired power)
- Wireless communication protocol
- Enclosure rating for environmental protection
- Installation method (bolt-on, adhesive, welded)
- Maintenance and calibration requirements
- Built-in analytics capabilities
Common Wireless Sensors for Wind Turbine Monitoring
What are the most frequently used wireless sensors in wind turbine monitoring? Two of the most common types are vibration sensors and temperature sensors.
Vibration Sensors
Vibration sensors measure equipment vibration to detect issues such as imbalances, loose components, misalignments, and bearing wear. Accelerometers and velocity transducers are commonly used technologies for this purpose.
Temperature Sensors
Monitoring temperature differentials allows for early identification of developing problems before failures occur. Fiber optic temperature sensors provide distributed temperature measurements along the length of the fiber, offering a comprehensive view of thermal conditions throughout the turbine.
Implementing a Comprehensive Monitoring Strategy
To maximize the benefits of remote monitoring, wind farm operators should develop a comprehensive strategy that integrates various sensor types and data analysis techniques. This holistic approach enables a more accurate assessment of turbine health and performance, leading to improved decision-making and operational efficiency.
Key Components of an Effective Monitoring Strategy
- Sensor selection and placement optimization
- Data collection and transmission protocols
- Real-time data processing and visualization
- Integration with existing SCADA systems
- Predictive analytics and machine learning models
- Alert and notification systems
- Regular system maintenance and calibration
Overcoming Challenges in Remote Monitoring Implementation
While the benefits of remote monitoring are clear, implementing such systems can present challenges for wind farm operators. Addressing these challenges is crucial for realizing the full potential of remote monitoring technologies.
Common Challenges and Solutions
- Data security concerns: Implement robust encryption and access control measures
- Integration with legacy systems: Develop custom interfaces or use middleware solutions
- Sensor reliability in harsh environments: Choose ruggedized sensors with appropriate IP ratings
- Data overload: Implement data filtering and prioritization algorithms
- Skilled personnel shortage: Invest in training programs and consider outsourcing analytics
The Economic Impact of Remote Monitoring on Wind Farm Operations
Implementing a comprehensive remote monitoring system can have a significant positive impact on the economic performance of wind farms. By optimizing turbine efficiency, reducing downtime, and lowering maintenance costs, operators can improve their return on investment and overall profitability.
Quantifying the Benefits of Remote Monitoring
How can wind farm operators measure the economic impact of remote monitoring? Several key performance indicators (KPIs) can be used to assess the effectiveness of a monitoring system:
- Increase in annual energy production (AEP)
- Reduction in unplanned downtime
- Decrease in operations and maintenance (O&M) costs
- Extended turbine lifespan
- Improved capacity factor
Case Studies: Successful Implementation of Remote Monitoring Systems
Examining real-world examples of successful remote monitoring implementations can provide valuable insights for wind farm operators considering such systems. These case studies highlight the practical benefits and lessons learned from deploying advanced monitoring technologies.
Case Study 1: Offshore Wind Farm in the North Sea
A large offshore wind farm implemented a comprehensive wireless monitoring system, resulting in:
- 15% reduction in unplanned downtime
- 10% increase in annual energy production
- 20% decrease in maintenance costs
- Early detection of gearbox issues, preventing catastrophic failures
Case Study 2: Onshore Wind Farm in Texas
An onshore wind farm in Texas deployed an AI-driven monitoring system, achieving:
- 8% improvement in overall turbine efficiency
- 30% reduction in false alarms for maintenance
- Predictive maintenance scheduling, reducing turbine downtime by 25%
- Increased lifespan of critical components by an estimated 2-3 years
Emerging Trends in Wind Farm Remote Monitoring
As technology continues to advance, new trends are emerging in the field of wind farm remote monitoring. These innovations promise to further enhance the efficiency and reliability of wind turbines, driving the industry towards even greater sustainability and profitability.
Drone-Based Inspections
How are drones revolutionizing wind turbine inspections? Unmanned aerial vehicles (UAVs) equipped with high-resolution cameras and thermal imaging sensors can perform detailed inspections of turbine blades and towers. This approach reduces the need for dangerous manual inspections and allows for more frequent and comprehensive assessments of turbine condition.
Edge Computing for Real-Time Analytics
Edge computing brings data processing closer to the source, enabling real-time analytics and faster decision-making. By processing data locally at the turbine level, operators can reduce latency and bandwidth requirements while improving response times to critical events.
Digital Twin Technology
Digital twins create virtual replicas of physical wind turbines, allowing operators to simulate various scenarios and optimize performance in a risk-free environment. This technology enables more accurate predictive maintenance and performance optimization strategies.
Regulatory Considerations for Remote Monitoring Systems
As wind farm operators implement advanced remote monitoring systems, they must navigate various regulatory considerations to ensure compliance with industry standards and government regulations.
Key Regulatory Areas
- Data privacy and security regulations (e.g., GDPR in Europe)
- Environmental impact assessments for new sensor installations
- Electromagnetic compatibility (EMC) standards for wireless devices
- Aviation safety regulations for tall structures
- Grid code compliance for power generation facilities
Training and Skill Development for Remote Monitoring
The implementation of advanced remote monitoring systems requires a workforce with specialized skills. Wind farm operators must invest in training and skill development to ensure their teams can effectively utilize these technologies.
Essential Skills for Remote Monitoring Personnel
- Data analysis and interpretation
- Predictive maintenance techniques
- Wireless sensor technology
- Cybersecurity fundamentals
- Machine learning and AI concepts
- SCADA system management
- Renewable energy regulations and compliance
The Role of Remote Monitoring in Grid Integration
As wind energy continues to play a larger role in the global energy mix, remote monitoring systems are becoming increasingly important for grid integration. These systems help wind farm operators manage power output more effectively, ensuring grid stability and reliability.
Benefits of Remote Monitoring for Grid Integration
- Improved forecasting of wind power generation
- Enhanced reactive power control
- Faster response to grid frequency fluctuations
- Better coordination with other renewable energy sources
- Increased overall grid reliability and stability
Cybersecurity Considerations for Wind Farm Remote Monitoring
As wind farms become increasingly connected and reliant on digital technologies, cybersecurity has become a critical concern. Protecting remote monitoring systems from cyber threats is essential to ensure the safety and reliability of wind energy production.
Key Cybersecurity Measures for Wind Farms
- Implement robust access control and authentication mechanisms
- Use end-to-end encryption for data transmission
- Regularly update and patch all software and firmware
- Conduct regular security audits and vulnerability assessments
- Develop and maintain an incident response plan
- Train personnel on cybersecurity best practices
- Implement network segmentation to isolate critical systems
The Future of Wind Farm Remote Monitoring: Integrating with Other Renewable Energy Sources
As the renewable energy sector continues to evolve, the integration of wind farm remote monitoring systems with other renewable energy sources is becoming increasingly important. This integration allows for more efficient energy production and grid management across diverse renewable energy portfolios.
Opportunities for Integrated Monitoring Systems
- Coordinated output management between wind and solar farms
- Optimized energy storage utilization
- Improved forecasting for hybrid renewable energy systems
- Enhanced grid stability through diversified energy sources
- Unified monitoring platforms for multiple renewable technologies
As wind farm remote monitoring technologies continue to advance, operators who leverage these innovations will be well-positioned to maximize efficiency, reduce costs, and contribute to a more sustainable energy future. By embracing comprehensive monitoring strategies and staying abreast of emerging trends, wind farm operators can ensure their facilities remain at the forefront of renewable energy production.
As wind energy continues to grow as a vital source of renewable power, wind farm operators face the challenge of maximizing turbine performance and efficiency. Implementing a comprehensive wireless remote monitoring system is critical for optimizing wind farm operations and profitability. Let’s explore why remote monitoring is so essential and how the latest technologies are transforming wind turbine management.
Real-Time Insights Optimize Turbine Operation
The ability to continuously monitor a wind turbine’s status provides operators with the data they need to identify issues early and take corrective action. Detailed performance metrics on factors like vibration, temperature, yaw alignment, and power output allows operators to fine-tune the turbine for peak efficiency. Subtle changes and anomalies can be detected before they lead to costly downtime and lost production.
For example, monitoring vibration through wireless sensors makes it possible to detect increased friction in the drivetrain before catastrophic failure occurs. Likewise, tracking temperature changes in the generator and lubrication oils can indicate developing problems long before an overhaul is needed.
Lower Costs Through Proactive Maintenance
With round-the-clock remote monitoring, maintenance can be performed proactively when needed rather than on a fixed schedule. This condition-based approach reduces maintenance costs by avoiding unnecessary service calls. Operators can also troubleshoot issues remotely, often negating the need to send out technicians.
By catching failures early, damage to components is minimized. Small repairs can be made promptly before issues escalate or secondary damage occurs. With longer running times between major overhauls, the lifetime of capital equipment is extended.
Why Choose Wireless Sensors?
Traditionally, wind turbine monitoring required running expensive copper cables from each tower to the operations center. New wireless sensor networks offer a flexible and scalable alternative without the high infrastructure costs.
Self-contained sensors can be easily mounted on the tower, rotor, and generator to collect vibration, temperature, strain, and other data. This information can then be transmitted wirelessly to the central control room for monitoring and analysis.
Real-Time Data Enables Predictive Analytics
By compiling longitudinal data from each turbine, operators can utilize predictive analytics tools to detect subtle performance deviations and forecast maintenance needs. Machine learning algorithms can automatically identify patterns that indicate an impending failure or required service.
For instance, monitoring systems can learn a turbine’s normal power curve based on wind speeds. Any deviations from this curve would then trigger an alert, allowing operators to address the issue promptly.
The Future Is Automated
Ultimately, the future of wind turbine monitoring will be highly automated systems with self-diagnostics and AI capabilities. The goal is to enable turbines to automatically detect threats, diagnose their own operational issues, and even dispatch technicians when on-site work is required.
As monitoring technologies continue to advance, onboard controllers will integrate real-time data analytics directly into turbine control logic. This will allow turbines to autonomously optimize their performance while mitigating wear and tear.
Wind farm operators that leverage the latest wireless monitoring capabilities today will be well-positioned to capitalize on the automated systems of tomorrow.
When designing a wireless monitoring system, choosing the right sensors is crucial. The sensors will determine what types of data can be collected from the turbines, which directly impacts the actionable insights operators will gain.
Choosing the Right Wireless Sensors for Data Collection
Several key factors must be considered when selecting wireless sensors for wind turbine monitoring, including:
- Data types needed – Temperature, vibration, strain, humidity, etc.
- Measurement accuracy and resolution
- Sensor operating conditions – Temperature, moisture, vibration
- Power requirements – Battery or wired power
- Wireless communication protocol
- Enclosure rating for environmental protection
- Installation method – Bolt-on, adhesive, welded
- Maintenance and calibration requirements
- Built-in analytics capabilities
Some of the most common wireless sensors used for wind turbine monitoring include:
Vibration Sensors
Vibration sensors measure equipment vibration to detect issues like imbalances, loose components, misalignments and bearing wear. Accelerometers and velocity transducers are commonly used technologies.
Temperature Sensors
Monitoring temperature differentials allows early identification of developing problems before failures occur. Fiber optic temperature sensors provide distributed sensing over a long turbine blade.
Wind Speed and Direction Sensors
Anemometers and wind vanes measure wind conditions to optimize turbine positioning and determine power output. LIDAR remote sensing is also used.
Strain Gauges
Strain gauges measure blade deformation from aerodynamic loading. This identifies areas of potential fatigue failure.
Generator Sensors
Current and voltage sensors provide generator performance data to evaluate power output and efficiency.
By leveraging a network of complementary sensors, operators gain visibility into the complete turbine environment for predictive maintenance and performance optimization.
During the design process, turbine manufacturers can provide input on optimal sensor types and locations based on their expertise. However, operators may also consider third-party monitoring solutions that can retrofit existing infrastructure.
The ultimate wireless monitoring system provides actionable intelligence in real-time, while remaining adaptable and scalable for future analytics capabilities.
Installing Sensors to Capture Wind Speed and Direction
Once the right sensors are selected, proper installation is key to collecting accurate and reliable data. Here are some best practices for installing wind speed and direction sensors on turbines:
Anemometers that measure wind speed are typically mounted on the back of the turbine nacelle. This placement provides exposure to winds approaching the rotor plane. Installing at hub height allows correlation with power output.
For redundant monitoring, additional anemometers can be placed on the front of the nacelle or at ground level on the tower base. Comparing wind speeds at different heights provides insights into wind shear.
Wind vanes must be positioned to avoid interference from the turbine structure. Common placements are on short booms extending sideways from the nacelle or the rear of the nacelle roof.
Proper alignment during installation is critical – wind vanes must be oriented correctly relative to geographic north and the rotor. Precision measurements during installation prevent errors.
An inclinometer should be integrated to measure tilt of the nacelle, enabling correlation of vane data with the true horizontal plane.
For optimal accuracy, sensors require proper cable termination and signal conditioning. Verifying output signals and calibrations after installation catches any wiring issues.
Wireless sensor transmitters allow flexibility in positioning without the need for long sensor cables. They can be powered by small solar panels or vibration harvesting to avoid battery changes.
Regular inspection and maintenance of sensors ensures continuous functionality. Anemometer bearings require occasional lubrication to avoid deterioration.
By following best practices for locating, installing, and maintaining wind sensors, operators can be confident in the accuracy of the wind data collected.
This data enables optimizing turbine positioning for maximum power production, and provides critical context for analyzing turbine performance.
Monitoring Vibration to Detect Early Signs of Failure
Vibration analysis is a critical component of any wind turbine health monitoring program. By tracking vibration, operators can identify issues early before they lead to catastrophic failures.
Sensors such as accelerometers are installed on key turbine components including the gearbox, generator, main bearings, blades, and tower. They detect abnormalities in vibration patterns that indicate developing faults.
For example, increased vibration in the gearbox can signal worn bearings, gear damage, or misalignment issues. Excess vibration in the generator may indicate winding problems, shorted laminations, or rotor bar cracks.
Blade vibration provides insights into imbalance, aerodynamic issues, and structural fatigue. Tower vibration can help identify foundation settlements or loose bolts.
Advanced monitoring systems utilize software to set configurable alarm thresholds for different vibration frequency bands. This allows fine-tuning to avoid false positives while still detecting real problems.
By analyzing vibration trends over time, issues can be identified at an early stage before equipment damage escalates. For example, a 20% increase in vibration may indicate a bearing moving towards failure.
Vibration monitoring is most effective when complemented by other sensor data. Correlating vibration anomalies with operating conditions provides context. For example, high vibration only during certain wind speeds may indicate blade flutter.
Effective monitoring requires establishing a turbine’s baseline vibration signature at commissioning to compare against. Signatures should be verified each time the rotor RPM changes.
Ongoing monitoring accounts for changes over time. Software analytics can track long-term increases indicating wear. Advanced systems even utilize machine learning to automatically identify deviations.
By enabling early diagnosis of developing issues, vibration monitoring reduces unplanned downtime and costly damage. This maximizes turbine reliability and profitability over the long term.
Regular field checks are still required to validate sensor data. But with wireless access to vibration metrics, operators can prioritize tasks based on actual condition rather than guesswork.
Vibration monitoring delivers actionable insights – helping operators optimize maintenance scheduling, improve availability, extend equipment life, and avoid catastrophic failures.
Tracking Temperature Changes in Real Time
Monitoring temperatures throughout the wind turbine provides critical insights into developing faults before they lead to failure. Subtle temperature changes often presage larger problems.
Key components to monitor include the generator, gearbox bearings, lubrication oil, hydraulics, transformers, and battery bank. Fiber optic sensors attached along the turbine blades provide distributed temperature measurement.
Sensors allow continuously tracking temperature fluctuations in real-time rather than periodic manual checks. Operators can remotely view thermal trends under different operating loads and ambient conditions.
Sudden temperature spikes often indicate an imminent failure. A 20°C rise in the generator winding temperature may signal deteriorating insulation. Higher than normal gearbox bearing temps can presage lubrication loss or wear issues.
More subtle temperature increases over time also provide early warning. A 3°C rise in hydraulic oil temperature over two months may indicate a developing issue like a blocked filter.
Monitoring software can automatically generate alerts when temperatures exceed predetermined thresholds. This enables a proactive response to mitigate damage.
Temperature data also helps optimize turbine operation. Analyzing blade thermal patterns allows pitch adjustment to avoid damaging icing conditions.
By tracking temperature differentials over time, developing hot spots and cold spots can be identified to guide preventive maintenance. Thermal imaging cameras help validate and visualize sensor data.
Properly calibrated sensors are essential for generating accurate temperature data. It’s critical to account for external factors like solar heating that could skew results.
Wireless temperature monitors with automated data logging simplify setup while providing flexibility. Latest sensors even utilize IoT connectivity for seamless data integration.
In summary, real-time temperature monitoring provides invaluable insights into developing equipment issues before they escalate into major failures. This allows mitigating damage and avoiding unplanned downtime.
Logging Wind Turbine Power Output Remotely
Monitoring a wind turbine’s power output is critical for optimizing performance and revenue. Remote monitoring systems allow continuously logging power metrics to identify issues promptly.
Power output depends directly on rotor speed, blade pitch angle, and generator efficiency. Changes in these parameters due to either control faults or component wear will reduce energy production.
Generator current and voltage sensors provide essential data for determining power output. Logging this in real-time rather than periodic manual recording provides a detailed picture.
With remote monitoring, each turbine’s output can be tracked on a minute-by-minute basis. Operators gain visibility into the turbine’s power curve and can detect underperformance.
For example, reduced current at certain wind speeds may indicate blade soiling, damage, or aerodynamic changes. Lower voltage could signify generator or transformer issues.
Monitoring systems can automatically correlate power data against other metrics like wind speed, blade pitch angle, and temperatures. This simplifies diagnosing the root cause of any output drops.
Power data is also critical for verifying proper control system function. The controller constantly adapts to maximize energy capture based on sensor inputs and algorithms.
Real-time monitoring helps assess if the turbine is truly optimizing power output as wind conditions change. Operators can identify any need for control software tuning.
Continuously logging output metrics enables utilizing advanced analytics. Historical data provides a baseline to compare against, highlighting underperformance.
Predictive algorithms can forecast expected power output based on weather forecasts. Significant deviations trigger alerts to potential grid instability from the wind farm.
In summary, remotely monitoring and logging power production data at regular intervals provides operators the visibility needed to maximize wind turbine performance and revenue.
By leveraging power output analytics, developing issues can be identified early before losses accumulate. This helps optimize efficiency and turbine life.
How Remote Monitoring Improves Turbine Reliability
Maximizing wind turbine reliability and availability is critical for profitable operation. Comprehensive monitoring provides the visibility required to proactively identify issues before they lead to failures.
Continuously monitoring critical components like the gearbox, generator, bearings, blades, and tower provides early warning of developing faults. Operators can address problems before they escalate.
For example, sensors may detect increased temperature and vibration in a gearbox bearing. This prompts a controlled shutdown for inspection and remediation before severe damage occurs.
Without monitoring, that bearing may have failed catastrophically resulting in a 3-month gearbox replacement. Instead, a 2-day bearing replacement prevents far larger losses.
Remote monitoring also enables optimizing turbine operation to improve reliability. Tracking blade icing in real-time allows properly adjusting blade pitch to avoid overload failures.
Analyzing performance data helps tune turbine control parameters and algorithms for peak efficiency under all conditions. This reduces wear-and-tear.
Continuous condition data provides a precise record of asset health. Operators can plan predictive repairs during scheduled shutdowns well before failure risk.
Monitoring key components like gearbox lubrication oil also facilitates moving from time-based to condition-based maintenance. This prevents needless costs for component overhaul at fixed intervals.
With remote access to reliable health data, technicians arrive onsite fully prepared with parts and tools. This improves first-time fix rates, minimizing repeats.
Detailed event logging assists root cause analysis of any failures that do occur. Problems can be addressed at the source to prevent recurrence.
In summary, comprehensive monitoring is instrumental for maximizing turbine availability, safety, and service life. This generates more clean power over decades of operation.
With condition visibility, failures become predictable and preventable. Remote monitoring is a key enabler for cost-effective wind turbine reliability.
Software and Analytics for Actionable Insights
The massive amount of data generated by wind turbine sensors is only useful if it can be analyzed to deliver actionable insights. Advanced monitoring software and analytics capabilities are key to unlocking the value of sensor data.
Monitoring platforms provide capabilities to ingest and process high-velocity streaming data from hundreds of turbine sensors in real-time. This enables identifying issues the moment they occur.
For example, software can continuously correlate vibration, temperature and load data to historical baselines to detect anomalies indicative of emerging failures. Operators are notified immediately to address the problem.
Machine learning algorithms enable assets to “learn” their own optimal operating envelopes. Any deviations automatically trigger alerts for investigation.
Digital twins created by the software integrate multi-parameter turbine data to visualize performance. Operators can manipulate parameters to simulate effects before deploying changes.
Analytics dashboards provide visibility into fleet-wide asset health and performance metrics. Data is distilled into trends, summaries, and visualizations for rapid insights.
Analytics also facilitates moving from reactive to predictive maintenance. Pattern recognition identifies degradation over time and predicts future failures based on data.
For example, a 3% rise in gearbox bearing temperature over two weeks may indicate impending failure in 1-2 months based on prior failure data patterns.
This predictive intelligence allows ample time for parts procurement and planning the optimal service window well before an urgent breakdown.
Powerful analytical models help optimize complex turbine control software for maximum efficiency under all operating conditions. This maximizes energy production.
In summary, advanced monitoring software and analytics transform raw sensor data into prescriptive insights that tangibly improve performance, reliability, and profitability.
Automating Alerts to Identify Issues Proactively
The volume of data generated by wind turbine sensors can be overwhelming for operators to monitor manually. Automated alerts that notify of issues in real-time are essential.
Modern monitoring systems allow configuring rule-based alerts for each sensor across the turbine fleet. Thresholds can be tailored to individual turbine models.
For example, operators can define rules to be notified immediately via text or email if:
- Gearbox oil temperature exceeds 75°C
- Nacelle vibration increases by 20% overnight
- Wind speed exceeds 25 m/s for over 1 minute
Alert rules can also correlate multiple sensor data to identify issues. An alert may trigger if generator RPM drops but wind speed is within normal range, signalling a control fault.
Machine learning algorithms automate alerting by analyzing historical turbine data to define normal operating thresholds. Any outlier triggers an alert for investigation.
Automated alerts ensure operators are immediately notified of potential faults before they escalate. Issues can be addressed promptly to prevent larger problems.
Alert rules must be carefully configured during system implementation to avoid alert fatigue. This involves optimizing thresholds and logic to minimize false positives.
Analytics dashboards provide visibility into the frequency and distribution of alerts across the turbine fleet. This facilitates continually tuning rules to strike the right balance.
Responding to alerts in a timely manner is critical to maximize value. Teams must follow standardized processes to investigate alerts and mobilize resources.
Automated escalations can notify additional personnel if an alert is not acknowledged within a defined timeframe. This ensures adequate coverage.
In summary, automated real-time alerts driven by sensor data and analytics deliver tremendous value by enabling a proactive response to developing turbine issues.
This transforms wind turbine monitoring from passive data collection into an active asset management tool that improves reliability and efficiency.
Integrating Remote Monitoring Data with Other Systems
To maximize value, data from wind turbine monitoring systems should be integrated with operational software, asset management platforms, and enterprise systems.
Typical integration points include:
- SCADA system – Monitoring data can supplement SCADA analytics for identifying performance issues.
- Turbine controller – Sensor data may feed into control logic to optimize turbine operation.
- Work order system – Alerts can automatically generate work orders for technicians to investigate issues.
- CMMS/EAM – Monitoring data can update asset health status and trigger preventive maintenance.
- Inventory system – Predictive parts usage forecasts can assist planning inventory.
- ERP/Accounting – Automated power generation data feeds into energy accounting.
Modern monitoring systems provide APIs to enable seamless integration. Data can be streamed directly to other platforms, or accessed on demand as needed.
SCADA systems may only poll turbine data every 5-10 minutes. Integrating high-resolution sensor data provides greater visibility between scans.
For example, monitoring vibration at 100 Hz rates can detect emerging gearbox faults well before the SCADA system.
Enterprise asset management systems leverage monitoring data to optimize maintenance. Analysis of temperature trends can forecast the need for coolant system service.
Ideally, integration enables bi-directional data flow. Work orders generated for technicians can be associated with originating monitoring system alerts for tracking.
Careful configuration avoids duplication of data when integrating multiple systems. Master data management ensures consistency.
Monitoring data lakes allow consolidating wind farm time-series sensor data from all systems in a central repository for deep analytics.
In summary, integrating remote monitoring with operational software and enterprise systems unlocks the full value of turbine health data.
This drives data-driven decision making across the organization, improving productivity, reliability and profit.
Leveraging Cellular and Satellite Connectivity
Getting monitoring data from offshore and remote wind farms relies on wireless connectivity. Cellular and satellite networks enable reliable data transfer.
Cellular networks provide the most cost-effective solution for wind farms in coverage areas. Standards like 2G, 3G, and LTE offer options to match bandwidth needs.
Cellular data transmission is ideal for periodic batches of condition data from turbines. For real-time monitoring, bandwidth may need to be shared between multiple turbines.
Cellular connectivity can be integrated into remote terminal units. Gateways aggregate data from turbines before transmission over cellular networks.
Satellite networks bridge sites outside cellular coverage. Satellite modems equipped on turbines transmit data to orbiting satellites for delivery.
Latency is higher with satellite networks depending on the orbiting satellites used. Geosynchronous satellites provide lower latency than low earth orbit satellites.
Weather resiliency is a key consideration for offshore wind farms. Heavy rain or snow can disrupt signal integrity. Diversity like dual SIM cards improves reliability.
Licensed radio frequencies can provide point-to-point links between turbines and shore-based gateways. These avoid public network congestion.
Microwave transmission offers high bandwidth for real-time monitoring of offshore turbines. But dishes must be precisely aligned between sites.
Meshed wireless transmission using turbines as data hops avoids single points of failure. But this increases turbine hardware costs.
Ultimately, the optimal communications architecture depends on bandwidth needs, turbine density, and cost. Hybrid wired and wireless approaches provide flexibility.
With the right strategy, wind farm operators can achieve resilient monitoring connectivity, even for remote assets.
Security Considerations for Wireless Transmissions
While wireless monitoring enables valuable data collection from wind turbines, it also poses potential cybersecurity risks that must be addressed.
Wireless signals can be intercepted by unauthorized parties to extract sensitive operational data or gain system access.
Strong encryption of wireless data transit should be implemented using standards like SSL/TLS to prevent eavesdropping. VPN tunnels provide added protection.
Authentication mechanisms like unique certificates ensure connected devices and users accessing the system are authorized. This prevents spoofing.
Monitoring network segmentation isolates it from the turbine control network and other OT systems. This limits damage if a security breach were to occur.
Microsegmentation provides granular controls between components within the monitoring network as well. This contains threats from propagating.
Security gateways act as centralized policy enforcement points for monitoring traffic flows. They block unauthorized communication attempts.
Whitelisting allows only known, approved traffic on the monitoring network. Attempted connections from unknown sources are blocked.
Device hardening techniques like disabling unused ports and protocols, implementing password policies, and installing antivirus reduce the attack surface.
Continuous network monitoring tools watch for anomalies like unusual data flows or connection spikes that may indicate an attack.
Penetration testing of the end-to-end monitoring system proactively identifies vulnerabilities to address before they are exploited.
With well-designed security policies and controls tailored to wireless monitoring risks, wind farm operators can protect their assets and data.
This enables realizing the benefits of remote monitoring securely, without introducing unnecessary cyber risks.
Remote Access for Emergency Shutdowns and Maintenance
While on-site personnel remain critical, remote access capabilities provide wind farm owners additional flexibility to respond quickly during emergencies or maintenance needs.
During hazardous weather conditions like severe storms, the ability to remotely monitor turbines in real-time helps identify damage or anomalies proactively.
If an issue is detected, remote emergency stop can be initiated to shut down one or more turbines before a failure cascade occurs. This minimizes damage.
These capabilities reduce reliance on site visits to manually inspect, identify, and respond to issues. Remote capabilities optimize personnel safety in dangerous situations.
For maintenance needs identified through monitoring, remote access allows teams to virtually troubleshoot and diagnose issues before dispatching technicians.
This enables proper planning of repair strategies, parts/tools requirements, crew assignments, transport logistics, and other elements for an efficient on-site visit.
Secure remote desktop access to turbine control systems allows engineers to upload software and firmware updates without travel. This reduces service costs.
Virtual inspections via on-turbine cameras with pan-tilt-zoom features permit visually verifying problems like blade damage that may be difficult to characterize remotely.
Augmented reality can even overlay sensor data like vibration hotspots on real-time video. This further enhances remote troubleshooting.
Of course, not every maintenance task can be performed remotely. But supplementing on-site work with remote access capabilities provides wind farm owners greater oversight and responsiveness.
With robust connectivity and cybersecurity controls, wind turbines can be managed and monitored effectively from centralized remote operations centers.
Reducing Costs Through Proactive Maintenance
Effective monitoring enables proactive maintenance strategies that reduce costs for wind turbine owners.
Traditional time-based preventive maintenance schedules components for overhaul at fixed intervals to minimize in-service failures.
But this can result in unnecessary maintenance when components exceed expected design life. Lifetime consumption monitoring provides better intelligence.
For example, gearbox lubricant analysis can quantify debris accumulation and chemical changes to safely extend oil change intervals.
Monitoring blade strain continually verifies structural integrity. Maintenance is only needed when alarming trends are detected versus arbitrary dates.
Proactive cleaning of blades prevents buildup based on leading edge erosion monitoring, not guesses.
Condition-based approaches optimize maintenance timing. Analytics predict failure probability for smarter scheduling.
Early identification of developing faults through monitoring also reduces repair costs. Replacing a minor part is cheaper than replacing an entire component.
Being able to plan repairs during scheduled outages is more economical than urgent mobilization during inopportune weather.
Monitoring reduces technician diagnostic time at the turbine. The problem is already characterized remotely upfront.
Plus, all needed tools, parts, and staffing can be prepared in advance rather than making multiple trips.
Ultimately, effective monitoring programs can yield 20-25% reductions in maintenance costs for wind turbine owners.
The savings compound over decades of operation at large wind farms. Proper implementation pays for itself many times over.
Monitoring transforms reactive repairs into profitable, data-driven asset management.
The Future of AI and Machine Learning for Wind Turbines
Artificial intelligence and machine learning will be transformative technologies for optimizing wind turbine performance through predictive modeling and automation.
Deep neural networks will analyze vast datasets from turbine sensors, SCADA systems, weather forecasts, and domain knowledge to model complex behaviors.
These AI models will be able to accurately forecast turbine degradation and proactively schedule predictive maintenance to avoid failures.
Machine learning algorithms will also optimize control parameters in real-time for peak efficiency based on weather, lifetime wear, and other variables.
Reinforcement learning will enable turbines to autonomously “learn” ideal operating strategies customized to their environment by experimenting and refining behavior.
As models mature, human operators will transition to more supervision-based roles, leveraging AI insights to strategize improvements.
Cloud-based digital twins will integrate robust data from thousands of sensors to mirror exact wind farm conditions for simulation.
Operators can test predictive scenarios on digital twins to evaluate responses prior to implementation on real turbines.
Edge computing will allow real-time execution of analytics directly on turbines for latency-sensitive applications like predictive maintenance.
5G and LPWAN wireless technologies will enable massive bi-directional data flows between turbines, edge devices, and cloud platforms.
Combined with IoT-connected advanced sensors, the quantity and fidelity of data for AI models will accelerate.
In summary, the future integration of AI, advanced connectivity, and edge computing will usher in smarter, more autonomous wind turbines.
This will maximize efficiency, reliability, and operating lifetime through predictive, data-driven intelligent automation.