Looking to Repair Your Work Boots. Find the Best Patch HereLooking to Repair Your Work Boots. Find the Best Patch Here
Introduction to Rubber Boot Repair
Got a pair of rubber boots with a hole or tear in them? Don’t toss them out just yet! With the right materials and techniques, you can easily repair rubber boots yourself and extend their life. Whether you need to patch a small puncture or seam split on a pair of Wellies or fix a huge gash in some rugged work boots, this guide will walk you through the rubber boot repair process step-by-step.
Assessing the Damage
First things first, take a close look at the damage on your boots. Is it just a tiny pinhole puncture or minor surface scrape? Or is there a large rip or tear that exposes the inner lining? Carefully examining the flaw will help you determine the best repair method. Small holes and scrapes can simply be patched over, while larger gashes will need patches applied inside and out. Also check if any seams have come apart – these can often be fixed with rubber cement rather than a patch.
Cleaning and Prepping
Before attempting any repairs, thoroughly clean the area around the damage using soap and water to remove all dirt, oil and debris. Allow the boots to dry completely. This will help the adhesive stick and create a long-lasting patch. If the tear is ragged with frayed edges, trim any loose flapping pieces of rubber with sharp scissors or a utility knife so you have a clean edge to work with.
Selecting the Right Patch Material
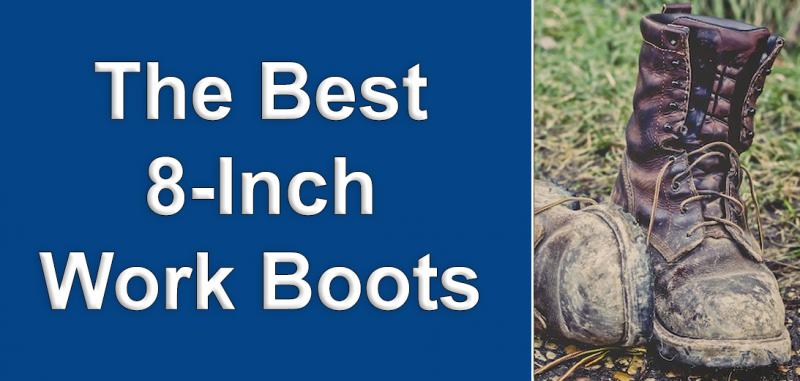
For the best results, the patch material should match the rubber on your boots as closely as possible. Look for patches made from natural rubber, neoprene or thermoplastic elastomers (TPE). Avoid patches with paper or fabric backings which won’t flex and bend with the boot. Try to find patches in a similar thickness and color to the surrounding rubber. Auto parts stores often sell quality rubber patches intended for flashings and seals that work perfectly for boot repairs. You can also order boot-specific repair kits online that include patches, glue and tools.
Applying a Patch
With your patch material selected, you’re ready to start repairing. Use sandpaper or an abrasive pad to lightly roughen both the patch and boot surface this will help the adhesive grip. Apply a thin, even layer of rubber cement to both surfaces and let it get slightly tacky before pressing them together. Rub firmly to adhere the patch in place, squeezing out any air bubbles. For larger holes, it’s best to apply a patch to the inside too for full reinforcement. Trim off any overhanging patch edges for a smooth finish. Remove any dried excess glue with rubbing alcohol.
Sealing the Edges
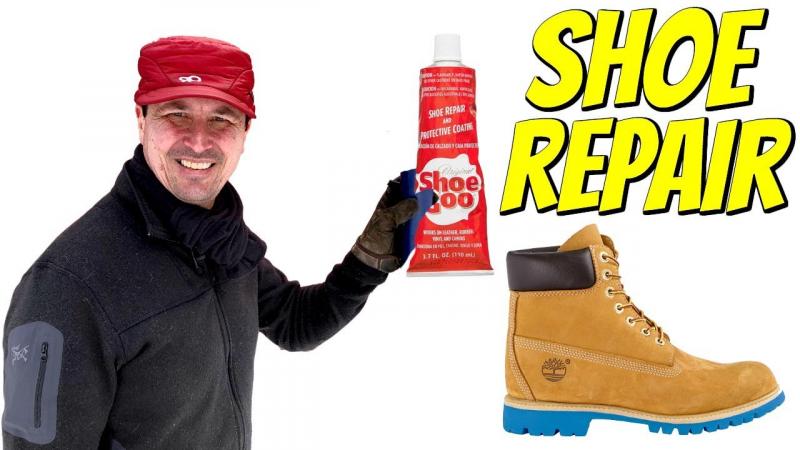
The final step is to seal down the edges of the patch to prevent peeling. Apply a thin bead of rubber cement around the border of the patch, letting it start to dry slightly before pressing down the edges smoothly. Wipe away any rubber cement oozing out around the patch with a rag. Allow the cement to fully cure for at least 24 hours before wearing the repaired boots.
Alternative Quick Fixes
For temporary emergency repairs, duct tape or Shoe Goo can patch holes and tears in a pinch. But these won’t be as durable or waterproof as a proper rubber patch. You can also try sealing small punctures by working rubber cement into the hole and letting it cure.
Tips for Successful Repairs
Patience is key – allow sufficient drying time when applying rubber cement and patches for maximum strength. Only attempt repairs in a clean, dry area with good ventilation. Repair splits in the rubber along seams from the inside first whenever possible. Use a rasp or file to roughen slick or shiny rubber before patching. When patching a large hole, overlap multiple patches for full coverage. Periodically re-cement peeling edges to get more life out of a patch. With care, even serious rips and gashes can be repaired to restore the function and durability of well-loved boots.
Don’t let a damaged pair of rubber boots stop you from getting outside! Armed with the right materials and techniques, you can easily extend the life of your favorite Wellies, muck boots or work boots. Repairing your own boots saves money and reduces waste – so patch them up and keep them going for years to come!
Why Do Work Boots Wear Out So Quickly?
Cleaning and Preparation
Before attempting any repairs, it’s crucial to clean the damaged area thoroughly. Use soap and water to remove all dirt, oil, and debris from the boot. Allow the boots to dry completely before proceeding with the repair. This cleaning process ensures that the adhesive will stick properly and create a long-lasting patch.
If the tear has ragged or frayed edges, use sharp scissors or a utility knife to trim away any loose flapping pieces of rubber. This will create a clean edge to work with, improving the overall quality of the repair.
Choosing the Right Materials for Boot Repair
Selecting the appropriate patch material is crucial for a successful repair. The patch should match the rubber on your boots as closely as possible for the best results. Let’s examine some key considerations when choosing repair materials.
Types of Patch Materials
- Natural rubber
- Neoprene
- Thermoplastic elastomers (TPE)
Avoid patches with paper or fabric backings, as these won’t flex and bend with the boot. Try to find patches that are similar in thickness and color to the surrounding rubber. Auto parts stores often carry quality rubber patches intended for flashings and seals that work well for boot repairs. Alternatively, you can order boot-specific repair kits online that include patches, glue, and tools.
Adhesives for Rubber Boot Repair
Rubber cement is the most commonly used adhesive for repairing rubber boots. It creates a strong, flexible bond that can withstand the movement and stress placed on work boots. Some repair kits may include specialized adhesives designed specifically for rubber repairs.
Step-by-Step Guide to Patching Rubber Boots
Now that you have the right materials, let’s walk through the process of applying a patch to your rubber boots.
- Roughen the surface: Use sandpaper or an abrasive pad to lightly roughen both the patch and the boot surface. This helps the adhesive grip better.
- Apply adhesive: Spread a thin, even layer of rubber cement on both the patch and the boot surface.
- Allow to dry slightly: Let the adhesive become tacky before pressing the surfaces together.
- Press firmly: Adhere the patch in place, pressing firmly to remove any air bubbles.
- Reinforce large holes: For bigger damages, apply a patch to the inside of the boot as well.
- Trim excess: Cut away any overhanging patch edges for a smooth finish.
- Clean up: Remove any dried excess glue with rubbing alcohol.
Sealing the Edges
To prevent peeling, it’s important to seal the edges of the patch. Apply a thin bead of rubber cement around the border of the patch. Let it dry slightly before pressing down the edges smoothly. Wipe away any excess cement with a clean rag. Allow the repair to cure fully for at least 24 hours before wearing the boots.
Quick Fixes for Emergency Situations
Sometimes you need a quick fix to get through the day. While these methods aren’t as durable or waterproof as a proper rubber patch, they can help in a pinch.
- Duct tape: Can temporarily patch holes and tears
- Shoe Goo: A flexible adhesive that can seal small damages
- Rubber cement: Can be worked into small punctures for a temporary seal
Remember that these are temporary solutions and should be replaced with a proper repair as soon as possible for long-term durability.
Tips for Successful Boot Repairs
To ensure your boot repairs are effective and long-lasting, keep these tips in mind:
- Be patient: Allow sufficient drying time for adhesives and patches.
- Work in a clean, dry area with good ventilation.
- Repair splits along seams from the inside first when possible.
- Use a rasp or file to roughen slick or shiny rubber before patching.
- Overlap multiple patches for full coverage of large holes.
- Periodically re-cement peeling edges to extend the life of a patch.
With care and attention to detail, even serious damage can be repaired, restoring the function and durability of your favorite boots.
Understanding Work Boot Wear and Tear
Have you ever wondered why your work boots seem to wear out faster than expected? Let’s explore some of the reasons behind this common issue.
Factors Contributing to Rapid Wear
- Quality of materials: Many mass-produced boots use lower-quality materials to reduce costs.
- Frequency of use: Daily wear in harsh conditions accelerates deterioration.
- Environmental factors: Exposure to chemicals, extreme temperatures, or moisture can break down boot materials.
- Improper care: Neglecting regular cleaning and maintenance can shorten boot life.
While modern boots may not last as long as those from previous generations, understanding these factors can help you choose more durable options and take better care of your work footwear.
Extending the Life of Your Work Boots
While repairs can help prolong the life of your boots, prevention is always better than cure. Here are some strategies to help your work boots last longer:
Regular Maintenance
- Clean your boots regularly to remove dirt and debris.
- Apply appropriate waterproofing treatments.
- Condition leather boots to prevent cracking and drying.
- Rotate between multiple pairs of boots to allow them to dry out between uses.
Proper Storage
Store your boots in a cool, dry place away from direct sunlight when not in use. Use boot trees or stuff the boots with newspaper to help them maintain their shape and absorb moisture.
Timely Repairs
Address small issues promptly before they become major problems. A small tear or loose seam can quickly turn into significant damage if left unattended.
Choosing Durable Work Boots
When it’s time to replace your work boots, choosing a durable pair can save you money and hassle in the long run. Here are some factors to consider:
Materials
- Full-grain leather: Known for its durability and water resistance.
- Synthetic materials: Can offer lightweight durability for certain applications.
- Rubber: Ideal for wet conditions but may not breathe as well as leather.
Construction
Look for boots with Goodyear welt construction, which allows for easier resoling and repair. Double or triple stitching on seams can also indicate a more durable boot.
Brand Reputation
Research brands known for producing high-quality work boots. While they may be more expensive initially, they often prove more cost-effective over time due to their longevity.
By investing in quality boots and maintaining them properly, you can significantly extend their lifespan and reduce the frequency of repairs or replacements.
Environmental Impact of Boot Repair and Maintenance
Repairing and maintaining your work boots isn’t just good for your wallet – it’s also beneficial for the environment. Let’s examine the ecological aspects of boot repair and maintenance.
Reducing Waste
By repairing your boots instead of replacing them, you’re keeping them out of landfills. This reduces the amount of waste produced and conserves the resources that would be used to manufacture new boots.
Lowering Carbon Footprint
The production of new boots involves significant energy use and carbon emissions. By extending the life of your current boots through repairs and maintenance, you’re indirectly reducing your carbon footprint.
Sustainable Practices
Embracing a repair-and-maintain mindset aligns with sustainable consumption practices. It encourages a shift away from the “throwaway culture” towards a more responsible approach to consumer goods.
While the environmental impact of a single pair of boots may seem small, the cumulative effect of many individuals adopting these practices can be significant.
When to Replace Your Work Boots
While repairing your work boots can significantly extend their lifespan, there comes a point when replacement is necessary. How can you tell when it’s time to retire your old boots?
Signs It’s Time for New Boots
- Compromised safety features: If steel toes are exposed or electrical hazard protection is worn away, it’s time for new boots.
- Worn-out soles: When the tread is completely smooth or the sole is separating from the upper, repairs may not be sufficient.
- Persistent discomfort: If your boots are causing consistent pain or discomfort despite repairs, it may be time for a new pair.
- Frequent repairs: When you’re repairing your boots more often than you’re wearing them, it’s probably more cost-effective to replace them.
Remember, while repairs can extend the life of your boots, safety should always be the top priority. If your boots can no longer provide adequate protection for your work environment, it’s time to invest in a new pair.
By understanding when to repair and when to replace, you can ensure that your work boots always provide the protection and comfort you need on the job. Whether you’re patching a small hole or shopping for a new pair of boots, taking care of your work footwear is an investment in your safety, comfort, and productivity.
Introduction to Rubber Boot Repair
Got a pair of rubber boots with a hole or tear in them? Don’t toss them out just yet! With the right materials and techniques, you can easily repair rubber boots yourself and extend their life. Whether you need to patch a small puncture or seam split on a pair of Wellies or fix a huge gash in some rugged work boots, this guide will walk you through the rubber boot repair process step-by-step.
Assessing the Damage
First things first, take a close look at the damage on your boots. Is it just a tiny pinhole puncture or minor surface scrape? Or is there a large rip or tear that exposes the inner lining? Carefully examining the flaw will help you determine the best repair method. Small holes and scrapes can simply be patched over, while larger gashes will need patches applied inside and out. Also check if any seams have come apart – these can often be fixed with rubber cement rather than a patch.
Cleaning and Prepping
Before attempting any repairs, thoroughly clean the area around the damage using soap and water to remove all dirt, oil and debris. Allow the boots to dry completely. This will help the adhesive stick and create a long-lasting patch. If the tear is ragged with frayed edges, trim any loose flapping pieces of rubber with sharp scissors or a utility knife so you have a clean edge to work with.
Selecting the Right Patch Material
For the best results, the patch material should match the rubber on your boots as closely as possible. Look for patches made from natural rubber, neoprene or thermoplastic elastomers (TPE). Avoid patches with paper or fabric backings which won’t flex and bend with the boot. Try to find patches in a similar thickness and color to the surrounding rubber. Auto parts stores often sell quality rubber patches intended for flashings and seals that work perfectly for boot repairs. You can also order boot-specific repair kits online that include patches, glue and tools.
Applying a Patch
With your patch material selected, you’re ready to start repairing. Use sandpaper or an abrasive pad to lightly roughen both the patch and boot surface this will help the adhesive grip. Apply a thin, even layer of rubber cement to both surfaces and let it get slightly tacky before pressing them together. Rub firmly to adhere the patch in place, squeezing out any air bubbles. For larger holes, it’s best to apply a patch to the inside too for full reinforcement. Trim off any overhanging patch edges for a smooth finish. Remove any dried excess glue with rubbing alcohol.
Sealing the Edges
The final step is to seal down the edges of the patch to prevent peeling. Apply a thin bead of rubber cement around the border of the patch, letting it start to dry slightly before pressing down the edges smoothly. Wipe away any rubber cement oozing out around the patch with a rag. Allow the cement to fully cure for at least 24 hours before wearing the repaired boots.
Alternative Quick Fixes
For temporary emergency repairs, duct tape or Shoe Goo can patch holes and tears in a pinch. But these won’t be as durable or waterproof as a proper rubber patch. You can also try sealing small punctures by working rubber cement into the hole and letting it cure.
Tips for Successful Repairs
Patience is key – allow sufficient drying time when applying rubber cement and patches for maximum strength. Only attempt repairs in a clean, dry area with good ventilation. Repair splits in the rubber along seams from the inside first whenever possible. Use a rasp or file to roughen slick or shiny rubber before patching. When patching a large hole, overlap multiple patches for full coverage. Periodically re-cement peeling edges to get more life out of a patch. With care, even serious rips and gashes can be repaired to restore the function and durability of well-loved boots.
Don’t let a damaged pair of rubber boots stop you from getting outside! Armed with the right materials and techniques, you can easily extend the life of your favorite Wellies, muck boots or work boots. Repairing your own boots saves money and reduces waste – so patch them up and keep them going for years to come!
Why Do Work Boots Wear Out So Quickly?
If you’re like most hard-working folks, you rely on a sturdy pair of work boots to get through long days on the job site. But even the burliest boots seem to give out faster than they should. Those treadless soles and busted seams leave you puzzled – why do work boots wear out so quickly?
Well, amigos, the tough truth is that work boots just aren’t made like they used to be. Back in grandpa’s day, boots were built thick and heavy, made to last for years of daily wear. These days, most mass-produced boots sacrifice durability for affordability. They’ll keep your feet dry for one season, maybe two if you’re lucky. But soon enough, it’s time to toss ’em and buy a new pair.
But there are a few other reasons those boots disintegrate quicker than a sandcastle at high tide:
1. Cheap Materials
Cowhide leather, thick rubber soles, and sturdy stitching – that’s the good stuff. But many work boot companies cut costs by using inferior materials that just can’t handle the grind. Synthetic leather and thin soles wear out faster, plain and simple.
2. Poor Construction
A quality pair of boots is crafted by skilled hands, not spit out by a machine. But fast fashion and mass production means bootmakers often take shortcuts. Shoddy construction leads to early breakdowns at the stress points – the heels, toes, and seams.
3. Daily Abuse
Work boots aren’t taking a leisurely stroll – you’re counting on them for maximal support and stability as you walk, climb, and hoist all day long. Constant friction underfoot slowly grinds down the tread. Toes get scuffed and worn kicking around job site debris. Oil, dirt, and cement take their toll on the leather. Hard work means hard wear.
4. Lack of Maintenance
When’s the last time you cleaned your boots, applied leather conditioner, or replaced worn laces? Most guys just toss ’em in the closet after a long day and call it a night. But that lack of TLC shortens their lifespan considerably. Just a few minutes of routine care makes a big difference.
Now listen here, hoss – occasional breakdowns are inevitable when you work boots like a mule. But following a few tips will help extend their lifespan so you get the most bang for your buck.
9 Tips to Make Your Work Boots Last
1. Buy for Durability, Not Style
Resist the urge to splurge on some fancy kicked just because they look cooler than plain ole work boots. Top-shelf leather and sturdy construction matter a lot more than fashion when it comes to durability.
2. Rotate 2 Pairs of Boots
Alternating gives each pair a chance to fully dry out before the next wear. Otherwise, constant moisture weakens the materials over time.
3. Use Boot Dryers
Pop those soggy socks and boots into a boot dryer overnight to extract every drop of moisture. Speed drying helps preserve leather and avoid mildew buildup.
4. Apply Protective Sprays
Coating the leather with silicone or wax-based sprays adds a protective barrier against water and chemicals. Reapply every few weeks to maintain effectiveness.
5. Clean and Condition Regularly
Gently wipe away dirt and debris after each wear. Follow up with a leather conditioner to keep materials supple and prevent cracking.
6. Replace Laces
Don’t wait for laces to fully snap – swap them out at the first sign of damage or fraying. Worn laces strain the eyelets, causing premature wear.
7. Use Orthotic Insoles
Quality insoles provide arch support and shock absorption, reducing stress on the boots with each step. Custom orthotics are best for comfort and stability.
8. Resole When Needed
Some boot repair shops can replace worn soles and heels, extending their life at a fraction of the cost of new boots.
9. Address Problems ASAP
Don’t ignore small rips or missing screws – those tiny issues lead to big breakdowns. Make timely repairs to avoid further damage.
Now listen up, buckaroos – if you just can’t resuscitate those dusty old boots, don’t get discouraged. Your feet deserve dependable protection, and you shouldn’t have to pay out the nose for it every 6 months.
The good news? There’s an easy, affordable way to keep your feet happy and your wallet fat. Let me tell you about it…
Looking to Repair Your Work Boots? Find the Best Patch Here:
Alright partners, no need to ride off into the sunset just yet. Before you toss those boots to the coyotes, have you considered patching them up? A little TLC can fix most common boot failures quickly and cheaply.
But not just any old patch will do. For the best results, you need an industrial-strength repair that bonds instantly, seals totally, and outlasts the boot itself. You need…drumroll please…the SB Foot Boot & Shoe Repair Kit!
Now don’t be fooled by flimsy store-bought patches that peel right off after a day or two. This heavy duty repair kit is made exclusively for hard-working footwear, engineered to handle the toughest conditions and keep on sticking.
It includes 4 flexible TPU patches and special Vulcanizing Cement that melds them to your boot or shoe for a seamless, permanent fix. Just peel, stick, and press firmly for 30 seconds – that’s it!
Built-in primer helps the incredible adhesive bond instantly to leather, rubber, vinyl, canvas – you name it. Once it grabs hold, that patch won’t budge even if a horse drags your boot around the rodeo ring.
So you can finally say adios to holes, rips, cracks, and missing chunks without saying goodbye to your boots. Vulcanized patches restore worn tread, seal sole separations, and reinforce busted seams stronger than new.
No more duck tape or glue gun hack jobs. These drover-tested patches offer heavy duty reinforcement, waterproof protection, and abrasion resistance better than the original boot.
Whether your work boots are cracked, leaking, or treadless, SB Foot patches have got you covered. They’ll breathe new life into those old boots for a fraction of replacement cost.
So don’t even think about grabbing new boots until you try patching up your current pair. Just slap a patch on worn spots at the first sign of damage, and you can easily double or triple their lifespan.
Quit wasting your hard-earned dollars on disposable boots year after year. Invest once in the SB Foot Repair Kit for a permanent, cost-effective boot solution.
Your boots, wallet, and feet will thank you! So ride on over to www.sbfoot.com and snag this miracle shoe repair kit today. Your soles will be smiling for miles to come.
Identify Damage on Your Boots
If you rely on a sturdy pair of work boots to get you through long days on the job site, you know how important it is to keep them in good condition. However, even the toughest leather or rubber boots take a beating with heavy use. Keeping an eye out for damage as soon as it appears can help you repair your boots before the problems get worse.
One of the first signs of trouble is when you start to notice unusual wear on the soles. Maybe the heels look lopsided or the treads seem dangerously smooth. These are indications that the soles need repaired or replaced. Don’t wait until you start slipping and sliding everywhere – get those boot soles fixed right away.
Inspect the upper part of your boots frequently for cracks or holes. Small cracks can be sealed with shoe polish or a leather filler product. Don’t let these cracks expand into larger holes that leave your feet exposed. For larger damaged areas, you may need to patch the leather. Carefully clean the area, apply shoe glue or rubber cement, and secure a patch of similar leather or suede over the hole.
Pay close attention to the seams on your boots as well. Re-stitching separated seams may require a cobbler, but you can reinforce stressed seams with shoe glue before they split open. Watch for frayed stitching and missing grommets too. Even small issues like these can turn into big problems if you aren’t diligent about making repairs.
While you’re checking for visible damage, don’t forget to inspect the interior of your boots. Peel back the liner and make sure the insole is still securely glued down. An unglued insole can slide around uncomfortably with each step. You may be able to simply re-glue it, or the insole may need replaced. Also check for protruding tacks, staples, or nails inside the boot that could hurt your feet.
Pick the Right Patch Material
Once you’ve identified damage that requires patching, select an appropriate patch material. Leather, suede, and rubber boot patches can all be purchased. Make sure the weight and texture closely match your boots.
For leather boots, opt for a leather patch. Look for top grain or full grain leather patches to get the most durable repair. Avoid bonded leather patches that easily crack or peel away. A suede patch is a good choice for suede boots as long as the weight matches. Heavier suede may be too stiff for a flexible boot shaft.
Rubber boot patches tend to hold up well when adhered properly. Choose a rubber patch that offers good traction if repairing a sole or heel area. For the upper boot, select a smooth rubber patch that won’t get hung up on your pants leg when worn. Another option for waterproof rubber boots is to use a patch of inner tube from a bicycle tire.
Prep the Surface
Careful preparation helps patches hold up over time. Start by thoroughly cleaning the damaged area with soap and water or a leather cleaner. Let it dry completely. Use an abrasive pad or sandpaper to rough up the surface, which helps the glue adhere. Try not to damage the surrounding areas.
Apply a primer or activate the adhesive on the patch according to package directions. Some patches work better with contact cement applied to both surfaces, while others use a peel-and-stick application. Glue both surfaces and let the adhesive become tacky before applying the patch.
Use a roller or your fingers to smooth the patch and push out any air bubbles between the surfaces. Clamping patches between two boards applies even pressure as the glue dries. Depending on the adhesive used, drying time may range from overnight up to 72 hours.
Reinforce the Edges
Patches often fail when the edges peel up. Reinforce them with stitching for the most durable repair. Use waxed thread or dental floss and a heavy duty needle. Stitch around the perimeter of the patch using a baseball stitch. Knot securely on the inside of the boot.
An alternate technique is to overlap the patch and contact cement the edge flap to the boot. Apply glue to the underside of the flap and smooth it down. Clamp the area with boards and let it fully cure before wearing the boots.
Edge sealants like shoe glue or clear nail polish also help reinforce patch edges. Apply a thin coat around the perimeter of the patch and let it dry completely. This seals the fabrics together.
Protect Your Repair
Regular care keeps your patched boots going strong. Condition leather boots frequently to avoid additional cracking. Use polish to touch up edges of leather patches and hide visible stitching. Rubber protectants maintain waterproofing and prevent rubber patches from drying out.
Rotate boots between wearings so they can fully dry out. Stuff boots with newspaper or shoe trees to help them hold their shape. Store boots out of direct sunlight and away from heat sources that can degrade adhesives and fabrics.
With attentive inspections and prompt repairs, you can keep your work boots in action for years past their expected lifetime. Don’t wait for a blowout or other serious damage. At the first sign of an issue, patch your boots before small problems get bigger.
Best Materials for DIY Boot Repair
Got a pair of boots with worn out soles or a hole that needs patching? Don’t toss them out! With the right materials and a bit of DIY know-how, you can easily repair your favorite boots and extend their life. Whether you need to resole your work boots or patch a hole in your hiking boots, this guide will walk you through the best materials to use for any boot repair project.
Choosing the Right Sole Material
When it comes to resoling boots, you’ll need to pick a sole material that matches the original sole on your boots. Here are some of the most common resole materials to consider:
- Rubber – Flexible and waterproof, rubber makes an excellent resoling material for work boots and hiking boots alike. It provides plenty of traction and withstands the elements well.
- Leather – Leather is a classic resoling material for dress shoes and boots. It’s sophisticated, durable, and ages well. Leather soles can be slippery when wet, so add a rubber topsole for extra traction.
- EVA foam – Lightweight and shock-absorbing, EVA foam is perfect for running shoes and athletic boots. It’s softer than rubber but still provides decent traction.
- Vibram – Vibram is a brand of hardy, rugged rubber compound made specifically for resoling outdoor footwear. It grips well in mud, snow, and other conditions.
Match the original sole material on your boots whenever possible for the best results. Bring your boots into a cobbler and ask for their recommendation if you’re unsure what material to use.
Picking the Right Patch Material
For patching holes and damaged areas on boots, you’ll need an adhesive patch made of durable material that withstands flexing and abrasion. Here are some top options:
- Rubber patches – Look for heavy duty rubber patches made specifically for boot repair. They flex well and waterproof the damaged area. Great for work boots.
- Suede patches – Color-matched suede makes for almost invisible repairs on suede or nubuck boots. Seal the edges with glue.
- Iron-on patches – These patches have an adhesive back so you can simply iron them onto damaged areas. Use high-heat glue for extra hold.
- Leather patches – Carefully cut leather patches in the same color and texture as your boots for discreet patching.
Make sure to select a patch in a color and texture that matches your boot material so the repair blends in seamlessly. Prepare the damaged area by sanding and cleaning before applying any adhesive patch.
Choosing the Right Glue/Adhesive
The right glue or adhesive is crucial for creating strong, long-lasting boot repairs. Here are some top options:
- Contact cement – Contact cement adheres instantly and works on most shoe materials like leather, rubber, and vinyl.
- Shoe repair epoxy – Two-part epoxies specially formulated for shoe repair provide a super-strong bond. Great for resoling.
- Polyurethane adhesives – Flexible polyurethane glues like Barge Cement work well for adhering soles or patches.
- Cyanoacrylate (super glue) – Good for quick fixes and small holes. Doesn’t stand up over the long term for heavy repairs.
Always check the glue or adhesive specifications to make sure it works with your specific boot materials and repair project. Allow adequate drying time for maximum strength and hold.
Helpful Tools for DIY Boot Repair
Having the right tools on hand will make your boot repair project much smoother. Here are some must-have supplies:
- Utility knife – For trimming patch edges or cutting soles.
- Abrasives – Sandpaper or a rotary tool to roughen surfaces before gluing.
- Rubber mallet – For tapping soles into place.
- Roller – Helps apply even pressure after gluing.
- Clamps – Clamp pieces together as glue sets.
- Solvent – For removing old adhesive residue.
- Measuring tape – Measure for precise sizing when cutting patches or resoling.
- Scissors – Cut patches, soles, or other materials to size.
Invest in quality materials and take your time, and you can often achieve professional-level repairs on your own boots. With the right patches, glue, and preparation, those boots will be restored to last another season or two. So before you bid farewell to your favor boots, see what some DIY elbow grease can do to fix them up.
Choosing the Right Rubber Patch
Looking to repair your work boots? A high-quality rubber patch can bring your favorite boots back to life. When that reliable pair finally develops a hole, don’t despair – with the right patching materials and techniques, you can easily repair them for further adventures. Here’s how to choose and apply the best rubber patch for your DIY boot repair project.
Heavy-duty rubber patches designed specifically for shoe and boot repair are your best bet for patching holes, worn spots, or damaged areas on leather, suede, or rubber work boots. The key is finding a rubber patch that matches the thickness and texture of your boot material as closely as possible for a seamless repair.
For leather work boots, look for patches with a leather-like finish on one side and raw rubber on the other side to adhere to the interior boot surface. For rubber rain boots or muck boots, solid rubber patches bond best. Bring your boot into the cobbler shop and have them help you select a color-matched rubber patch blend right in.
Prep the damaged area by gently sanding to rough up the surface for better adhesion. Use scissors to trim the patch to match the hole size and shape. Apply a flexible boot repair glue like Barge Cement to both surfaces, allow to tack up, then firmly press the patch in place, smoothing from the center outward and applying even pressure.
You can even stack multiple layers of rubber patches for a seriously heavy duty repair. Just be sure to let each layer dry thoroughly before adding the next. A roller helps squeeze out air pockets for a tighter bond. Clamping the patch for a few hours as the glue cures will ensure maximum hold.
For quick trailside repairs, self-adhesive rubber patches can be ironed or heat-sealed onto damaged areas. Carry a few in your pack as emergency boot fixes until you can do a more permanent patch job at home. Those sticky patches combined with some sturdy waterproof tape can temporarily plug holes to keep feet dry.
With the right rubber patch and repair techniques, you can easily add more miles to those favorite boots. Once patched up, protected the area from further wear and abrasion by applying a flexible boot sealant. Investing a little time and effort into a DIY repair beats buying expensive new boots. So next time your soles spring a leak, reach for the rubber patches and glue – with a few simple steps, you’ll be back on the trail in no time.
Prepping the Boot Surface for Patching
Ready to revive those worn work boots with some DIY patching? Proper surface prep is crucial for getting patches and repairs to stick. So before gluing on any rubber, leather, or suede patches, take the time to properly prepare the damaged area for long-lasting bonds.
Start by thoroughly cleaning the area to remove any dirt, grease, or debris so patches will adhere tightly. Use a bit of dish soap and warm water and gently scrub with a small brush. Rinse and let dry completely.
Pro Tips for Applying the Rubber Patch
You’ve prepped the surface, chosen the perfect patch, and have your adhesive ready. Now comes the moment of truth – flawlessly applying that rubber patch to your damaged boots. Follow these pro tips and techniques for smooth, seamless DIY patching.
Less is more when applying boot repair adhesives. Thin, even layers are best to prevent oozing and sliding as you position the patch. If using a liquid cement like Barge, apply with a small stiff-bristled brush. For glue sheets, roll them out evenly with a brayer.
Allow the adhesive to become slightly tacky on both surfaces before joining – usually just a few minutes. You want it sticky but not fully cured. If it’s too wet, slippage can occur as you place the patch.
Carefully align the patch and press into place from the center outward to avoid trapping air pockets. Use a roller, your fingers, or the handle of a spoon to apply gradually increasing pressure, working the patch into full contact with the boot surface.
Once set, go around the edges of the patch with glue to seal them down fully. Then taper the edges by lightly sanding to help blend the patch.
For an extra-strong bond, you can layer patches and adhesives. Apply the patch as normal, allow to cure, then add another thin glue coat and second patch on top, offsetting the seams.
If there are any pinholes or gaps in the patch adhesion, dot them individually with superglue. A tiny dab seals the spot without making a mess.
Be patient during curing times – resisting the urge to wear the newly patched boots right away. Allow all adhesives to fully cure (12-24 hours) before subjecting boots to wear and tear.
Properly prepping the surface, precisely applying adhesive, and gradually building pressure as you set the patch gives you the best shot at a seamless, long lasting patch. Take it slow and follow these tips, and your favorite boots will be revived and ready for many more miles of wear.
Securing the Edges for a Tight Seal
You’ve got your rubber patch firmly adhered to fix that worrisome hole or crack in your favorite boots. But don’t stop there – properly finishing the edges is key for a repair that withstands the long haul. Here’s how to secure those patch edges for maximum longevity.
Once the main patch is set, brush or roll glue along the entirety of the exposed edges. This seals down the perimeter to prevent moisture from sneaking underneath and loosening the bond over time. Focus on the most vulnerable spots – the toe and heel of the sole, flex points, and patch corners.
Letting the Rubber Cement Cure Properly
When it comes to repairing and patching up your favorite pair of work boots, having the right supplies is key. But just as important is understanding how to use those supplies properly, especially when it comes to rubber cement. Allowing rubber cement to cure completely before proceeding to the next step is crucial for creating a strong, durable bond that will hold up to heavy use.
If you’ve ever made the mistake of not letting the rubber cement cure fully, you know the frustration that follows. The patch peels up immediately or separates from the boot after just a few wears. But don’t worry, we’ve all been there! With some patience and knowledge of the curing process, you can ensure your boots get a repair that will last.
Why Proper Curing is Essential
Rubber cement contains solvents that need to evaporate before the adhesive can set and bond two surfaces together. If you try to apply a patch before the cement has cured, the solvents prevent the adhesive from making full contact with the boot and patch material. The result is a weak bond that just can’t withstand rugged wear and tear.
Curing time allows the solvents to evaporate completely, leaving the thickened rubber adhesive behind. This adhesive will be soft and pliable initially, making it easy to press the patch into place. But after some time out in the open air, the adhesive hardens and develops a strong, durable grip.
Factors That Impact Curing Time
Several key factors determine just how long you need to let rubber cement cure:
- Temperature – Colder temperatures slow curing time. Warmer temperatures speed it up.
- Ventilation – Good airflow evaporates solvents faster.
- Thickness – Heavy applications take longer to fully cure.
- Surface – Non-porous materials like leather slow evaporation.
There are some general guidelines you can follow based on temperature, but monitoring the cement and doing a quick test is the best way to confirm it’s ready. We’ll go over both methods so you can get a feel for when your rubber cement is cured and primed for patching.
Following General Temperature Guidelines
As a general rule of thumb, here are the approximate curing times for rubber cement at different temperatures:
- 60-70°F – 30 to 60 minutes
- 50-60°F – 60 to 90 minutes
- 40-50°F – 90 to 120 minutes
So in a typical indoor environment around 70°F, you’ll want to wait about 30 to 60 minutes before applying your patch. If working in a cooler garage around 55°F, give it an hour to an hour and a half. The thickness of the cement layer will also impact the timeline. A thin coat may only need 30 minutes, while a thicker application could take the full 60 minutes.
For outdoor repairs in cooler weather around 45°F, wait at least an hour and a half before patching. Again, monitoring the cement and doing a test will give you the best sense of when it’s ready.
Doing a Quick Test
The most foolproof way to know if the rubber cement is cured is to touch it and do a quick test. Here are some signs it’s ready for patch application:
- No longer transfers to your finger when touched
- Does not feel cold or wet to the touch
- Has a noticeably thicker texture
- Patch material adheres easily when pressed into place
You’ll notice the cement is initially wet with solvents and will stick to your fingers. Once cured, it will feel dry to the touch. Press a small scrap piece of patch material into the cement and see if it sticks. The material should bond easily when pressed firmly into the adhesive.
If the cement still seems wet, cold, or tacky, give it more time. Continuing to let it cure in a well-ventilated area until it passes the finger test will ensure your patch gets the strongest adhesive power possible.
Applying the Patch
Okay, so you’ve let the rubber cement fully cure and it’s passed the tests. Now it’s ready for patch application. Just follow these steps:
- Cut the patch material to size, making sure it extends at least 1 inch beyond the damaged area.
- Align the patch over the damage and press it firmly into the cured cement.
- Apply pressure for 60 seconds or more to secure a strong bond.
- Trim any excess patch material around the edges.
That’s it! As long as you allowed ample curing time, the patch should remain firmly bonded as the cement finish hardening. Let it continue to cure uncovered for 6 to 12 hours after application for maximum strength.
Avoid These Curing Mistakes
Now that you know the right way to let rubber cement cure, here are a few common mistakes to avoid:
- Not allowing enough time – Rushing the process leads to weak bonds.
- Applying in cool temps – Colder weather can double or triple cure times.
- Patching in an unventilated area – Solvents evaporate slower without airflow.
- Applying too thick – Thin even layers cure fastest.
- Not testing before patching – Do the finger/patch test first.
With the helpful tips in this article, you can avoid these missteps and start repairing your boots with confidence. Just remember: patience and proper curing leads to long-lasting patches that will keep your footwear going strong. Check that cement and take your time—your boots will thank you!
Looking to Repair Your Work Boots? Find the Best Patch Here:
If you rely on your work boots every day, it’s only a matter of time before they start showing some wear and tear. Ripped seams, holes in the leather, separated soles – the damage can really add up. But before you toss your favorite boots out, consider repairing them with a high-quality patch.
With the right materials and some basic DIY skills, you can often extend the life of your boots and save some money in the process. When choosing a patch, make sure to pick one designed specifically for work boots. Here’s what to look for:
Purpose-Built for Work Boots
Patches made for shoes or casual boots simply won’t cut it when it comes to the demands of work footwear. Look for patches marketed as work boot repair patches or those made from extra tough materials.
Durable Materials
The best patches use heavy duty materials that can withstand job site conditions. Top options include:
- Thick rubber – Flexible and waterproof.
- Ballistic nylon – Resists abrasions and tears.
- Leather – Blends into boot material.
Make sure the adhesive on the patch bonds well to leather, rubber, and other work boot materials.
Heavy Duty Construction
Components like reinforced edges and corners go a long way toward patch durability. Multi-layer and self-vulcanizing patches also offer enhanced longevity.
Waterproof Capabilities
Patches made from non-porous materials like rubber can keep your feet dry, preventing moisture damage from repeating the same destruction.
Matches Boot Design
Look for patch shapes, textures and colors that closely match your boots. This helps the repair blend in rather than stand out.
With the right patch, you can fix rips, cover logos, reinforce seams and add toe/heel caps. Here are some top-rated work boot patch options to consider:
- Gear Aid Freesole Patch – Versatile for soles, toes, tears
- Friendly Swede Shoe Repair Kit – Multiple leather & nylon patches
- Dr. Martens Wonder Balsam – Conditions & seals leaks
Before patching, make sure the boot surface is clean and dry. Rough up smooth areas to help the adhesive grip. Apply rubber cement to both surfaces and let cure. Carefully align the patch and press firmly in place. Add sealant along the edges for extra holding power and waterproofing.
With the proper materials and some handy work, you can often extend the life of your favorite boots considerably. So next time your work footwear starts looking worse for wear, reach for a patch and get back to the job site in your trusty boots.
Adding Additional Layers for Heavy Damage
When your work boots have seen better days, don’t be tempted to just slap on a quick patch and call it good. For heavy duty damage, a single patch layer often isn’t enough to provide a lasting repair. The key is adding extra layers of reinforcement to distribute stress over a wider area and prevent future cracks or separations.
It may seem like overkill, but buffers of additional patch material around and beneath the main repair can make a huge difference in longevity. With the right technique, you can build up a durable patch “sandwich” that will keep those boots in action.
Start with the Base Layer
The first step is providing a solid foundation on which to build your layered patch. Cut a base patch from durable rubber or nylon material that extends at least an inch beyond the damaged area on all sides.
Roughen up the surface of the boot where this base layer will adhere. Then apply a coat of rubber cement and let it become tacky. Press the base patch into place with firm pressure, smoothing out any air bubbles.
This initial patch takes the brunt of the wear and provides a surface for additional layers to stick to.
Build Up Buffer Layers
Now you can start adding buffer pieces around the damaged area to distribute stress. These buffer patches should overlap the base layer by at least half an inch on all sides.
Cut small triangle or square shapes from rubber/nylon patch scraps. Apply cement to the underside of the buffers and the boot surface. Stick them in place surrounding the damaged spot, overlapping slightly.
Add as many buffers as needed to provide ample reinforcement. Two or three layers is usually sufficient, but highly damaged areas may need more.
Finish with the Top Patch
Finally, cut your visible top patch to size so it covers the damage and overlaps the buffer border completely. Coat the underside of the top patch with cement, let it become tacky, then press it into place over the buffer layers.
The top patch ties everything together, providing a new tread/exterior surface. Solid edge stitching gives added strength when patching along seams.
By starting below the surface and building up, you create a patch “sandwich” able to withstand far more wear than a single layer.
Tips for Success
Follow these tips to ensure durable multi-layer patches:
- Use sandpaper or knives to scuff up bonding surfaces
- Apply cement thinly and evenly to all layers
- Let cement become tacky before pressing patches in place
- Use a roller to smooth out bubbles and ensure adhesion
- Add sealant along patch edges for extra holding power
Take the time to properly build up your patch, applying each layer with care. The end result will be a fortified repair ready to deliver long-lasting performance.
Know Your Limits
While extra patch layers often do the trick, some damage is beyond DIY repair. Seek professional help if:
- Tears or holes span more than a few inches
- The sole is separating from the upper
- Internal stitches or supports are broken
- You’ve patched repeatedly and issues persist
Attempting overly-ambitious repairs that require replacing major boot components rarely pans out. At that point, replacement is the prudent option.
But for more moderate damage, building up durable patch layers can add months or even years of life back into worn work boots. With the right materials and technique, your footwear can soldier on through many more work days.
Looking to Repair Your Work Boots? Find the Best Patch Here:
If you rely on your work boots every day, it’s only a matter of time before they start showing some wear and tear. Ripped seams, holes in the leather, separated soles – the damage can really add up. But before you toss your favorite boots out, consider repairing them with a high-quality patch.
With the right materials and some basic DIY skills, you can often extend the life of your boots and save some money in the process. When choosing a patch, make sure to pick one designed specifically for work boots. Here’s what to look for:
Built for the Demands of Work
Patches made for casual footwear just don’t cut it when it comes to the rigors of industrial and construction work. Opt for those marketed as heavy duty work boot patches.
Tough, Durable Materials
Look for patches constructed from materials such as:
- Thick, rugged rubber
- Industrial-grade nylon
- Full-grain leather
The patch should also have a strong adhesive that bonds well to work boot materials and tread.
Reinforced Edges
Patches with reinforced stitching or piping around the outer edges are less likely to peel away or detach prematurely.
Waterproof Capabilities
Waterproof rubber and sealed seams prevent moisture from seeping in and degrading the repair.
Matches Existing Materials
Look for patch textures, colors and designs that closely match your boots. A seamless appearance blends better.
With the right patch product, you can fix ripped seams, toe caps, logos, tread and more. Here are some top-rated options:
- Gear Aid Freesole Patch
- 3M Leather and Vinyl Repair Kit
- Dr. Martens Wonder Balsam
Prep the damaged area, roughing up smooth surfaces. Apply adhesive to both patch and boot. Allow proper curing time. Press the patch firmly into place along all edges. Add sealant for extra security and water resistance.
With quality materials and some simple repairs, your favorite boots can tackle many more miles. Next time your work footwear starts looking beat up, reach for a patch and breathe new life into those hardworking kicks.
Patching Tips for Smooth Finishing
If you’ve ever had a hole wear through the toe or side of your favorite pair of work boots, you know how frustrating it can be. While duct tape may seem like a quick fix, it often peels off or leaves an uneven surface. For a more permanent and professional patch job, follow these tips to smoothly repair your worn work boots and get more mileage out of them.
Prepare the Area
Start by thoroughly cleaning the area you plan to patch using a stiff bristle brush and soap and water to remove any built-up dirt, oil or grease. This allows the patch to properly adhere. If the hole goes all the way through the leather or fabric, place a piece of masking tape on the inside of the boot temporarily to cover the hole from the inside.
Use a utility knife or razor blade to trim any loose threads or frayed edges around the damaged area so you have a clean foundation for patching. Lightly sand the area with fine grit sandpaper to rough up the surface a bit—this gives the patch something to grip. Wipe away any dust with a clean cloth.
Select the Right Patch Material
For leather boots, choose a patch made of suede or leather that closely matches the color and texture of the boot material. For fabric boots, look for an iron-on patch or adhesive patch made of a similar weight fabric. You can buy these pre-made patches online or at craft stores in different colors and sizes. Make sure to select a patch that extends at least 1⁄2-inch beyond the damaged area for the best seamless look.
If you can’t find a ready-made patch in the right color, consider using a fusible bonding web tape, which looks like a roll of sheer double-sided tape. Simply place a piece of scrap leather or fabric over the bonding tape, fuse it with an iron, and cut a custom patch to size. The heat activates the glue on the tape to bond your patch material.
Cut the Patch
Lay your patch over the damaged area and use a fabric pencil or chalk to trace the outline. Remove the patch and use sharp scissors to carefully cut along the outline. Cut slightly inside the outline so the patch is a bit smaller than the traced line. You want the patch to fit seamlessly within the damaged area. Snip diagonally into the corners so they don’t bunch up when patching.
Seal the Edges
To prevent the patch edges from peeling or fraying over time, it’s important to seal them. If you’re using an iron-on patch, the adhesive backing often creates a good seal when fused. For patches without adhesive, you’ll need to carefully apply a sealant around the edges and let it dry thoroughly.
For leather, a leather glue or rubber cement works well to seal the edges and prevent unraveling. Use a small brush to thinly coat around the edge of the leather patch then let it dry completely—usually about 30 minutes. Be sure to apply in a well-ventilated area.
On fabric patches, a fabric glue or even clear nail polish can seal the edges to prevent fraying. Again, use a small art brush and apply a thin, even layer around the edge and let fully dry before proceeding.
Affix the Patch
Now comes the fun part—attaching the patch! If using an iron-on patch, simply follow the product instructions for heat application. Usually, you’ll place a damp cloth over the patch, then apply a hot iron for 30-60 seconds. Check the progress frequently and don’t overheat.
For adhesive patches, peel away the backing paper and firmly press in place from the center outward to smooth any bubbles. Rub firmly around all edges. You may need to apply even pressure by placing a book or other weight on top for an hour or so as it bonds.
On leather patches without adhesive backing, apply a thin layer of rubber cement or leather glue to the back of the patch and boot area, let it become tacky, then firmly press together starting from the center. Use an up and down rubbing motion to smooth. Wipe away any excess glue along the edges. Weight it down as needed while the bond sets.
For fabric, use a fabric glue like Bish’s Original Tear Mender, following product directions. Apply a thin layer to the wrong side of the patch and boot area, wait until tacky, then press together while smoothing from the center outward.
Blending the Patch
Once your patch is solidly adhered, the final step is blending it into the surrounding material so the repair is practically invisible. For leather boots, use a bone folder or other dull tool to gently rub along the edges, pressing the patch into the boot leather to create a smooth transition.
On suede or rough-out leather, very lightly brush the edge perimeter with fine grit sandpaper to fuzzy up the edge and blend with the nap of the surrounding suede. Be very careful not to overdo it.
For fabric boot patches, the lighter the touch the better. If needed, gently needle along the edges to buried any visible stitching. The goal is for a seamless look.
If the color doesn’t perfectly match, applying a light coat of matching leather dye, acrylic paint or fabric paint along the patch edge can help it seamlessly blend with the surrounding boot material. Let it fully dry, then buff lightly with fine grit sandpaper.
And that’s it! Follow these patching tips and you can repair worn spots on your favorite boots rather than relegating them to the trash. With a bit of time and care, you can extend the life of your boots and keep your feet supported, protected and ready for work.
Preventing Future Wear and Tear
After patching up a worn out pair of work boots, you want them to last as long as possible before needing repairs again. While no boot lasts forever, there are things you can do to reduce wear and tear and extend their lifespan. Here are some handy tips to keep your boots in working order longer.
Rotate Your Boots
If you wear the same pair of boots day in and day out for work, it’s no wonder they wear out quickly. The constant flexing and pressure on the same spots every day can break down boots fast. Make it a habit to rotate between at least 2-3 pairs regularly. Letting boots fully dry out and “rest” between wears reduces the stress and strain on the materials so they last longer.
Use Boot Trees
Boot trees are shaped inserts that slide inside your boots when not being worn. The trees hold the boots upright, maintain the toe shape, and absorb interior moisture and odor. Allowing boots to sag and crumple can degrade the structure and materials over time. Trees preserve the form so boots wear evenly and don’t develop creases that can crack.
Cedar wood trees have natural moisture wicking properties to dry out the interior. Plastic trees also work well. Insert trees any time boots are off your feet to make them last.
Clean Regularly
Don’t let dirt, mud, chemicals or manure cake onto your boots. Hose or brush off exterior grime after each wear once boots have dried. Then clean the interior every few weeks with a small amount of mild soap and water on a sponge or soft brush. Rinse and dry thoroughly.
For odor, sprinkle some baking soda inside overnight to absorb smells before knocking it out. Keeping boots clean prevents abrasive particles from wearing down the leather and stitches prematurely.
Treat With Conditioner
Leather boots need occasional conditioning to keep the material supple and prevent cracking. Use a leather conditioner every few months, applying a thin layer and letting it soak in fully. For suede boots, use a suede brush to revive the nap.
Avoid over-conditioning which can weaken stitching and cause the leather to stretch. Let boots dry completely between wears after conditioning.
Weatherproof
Treating boots with a weatherproofing spray protects against moisture damage. The oils in the spray make leather and seams water resistant and prevent salt and chemical stains. Re-apply every few months as needed, spraying evenly and wiping away any excess.
Silicone sprays also help repel water and condition the leather. Be sure to do any weatherproofing outside and allow boots to fully dry before wearing.
Re-Lace
Inspect boot laces regularly and replace immediately if any fraying, damage or stretching occurs. Old laces that are stretched out or frayed will rub and abrade the eyelets each time you lace up, wearing them down over time.
New, snug fitting laces also ensure boots stay firmly tied and secured to your feet to prevent excess movement that can degrade materials.
Add a Toe Cap
The toe of a boot typically gets the most abuse and is the first area to wear out. Adding a rubber toe cap or toe guard provides an extra shield against scuffs and abrasion. Look for caps that adhere securely with strong construction adhesive and provide maximum coverage.
Toe guards screwed into the sole also work well. Replace caps immediately if they start peeling or come loose.
Use a Boot Dryer
Wet boots lead to accelerated breakdown of stitches, warping of leather and sole separation. Speed drying after each wear by placing boots on a boot dryer overnight, which gently blows warm air inside.
You can find inexpensive dryers online or at sporting goods stores. Rotate boots on the dryer to hit both the toe and heel until fully dry inside and out.
Add Insoles
Quality insoles provide essential arch support, shock absorption and cushioning. This enhances comfort and prevents excessive wear on boot linings. Look for insoles designed specifically for work boots to handle tough conditions.
Replace insoles every 4-6 months or when worn out. Letting boots fully air out between shifts keeps insoles fresher too.
With some TLC and preventative maintenance, you can keep your favorite boots in working order longer after repairs. Don’t wait for big holes to develop – be proactive with these tips for extended use.
When to Call in a Professional for Repairs
Doing minor patches and fixes on your own can extend the life of worn work boots. But there comes a time when the damage is beyond what you can handle at home. Calling in a professional for boot repair is worth it to restore their functionality, safety and comfort.
Structural Damage
Once the structure of the boot itself is compromised, it’s risky to wear them, and a professional repair is needed. This includes cracked leather uppers, damaged or separated soles, broken steel toes, worn out linings, and ripped open seams.
Attempting structural DIY fixes with adhesives or stitching often fails quickly. Boot makers have the skills, tools and industrial machines to properly mend upper, sole and lining damage.
Heel and Sole Replacement
Worn down soles with minimal tread left seriously reduce traction and can be unsafe on the job. Loose heels alter your gait and cause back/joint pain. Re-soling and re-heeling require specialty equipment to grind off and securely bond new soles/heels.
A good boot repair shop can replace just the heel or the entire sole depending on wear. Trying this yourself risks damage and improper bonding.
Toe Cap Rebuilds
Rubber toe caps eventually wear through with constant scuffing. Boot makers can remove old caps and adhere new ones for full toe coverage. They have heavy duty adhesives that hold securely.
Toe guards can also be re-screwed into the sole if loosening. A professional touch ensures it’s done right.
Lace Eyelet Repair
Eyelets that are pulled out or ripped open make lacing a chore. A shop can re-set eyelets by boring new holes and using a specialty machine to install metal or nylon eyelet grommets securely.
They can also replace broken speed hooks and install new custom laces that won’t fray.
Steel Toe Repair
Cracked or exposed steel toes put your feet at risk of injury and compromise safety. Attempting a home fix is difficult. Experts can smooth out dents, re-coat for corrosion protection, and replace cracked caps.
Some can even custom form new steel caps and liners to restore toe integrity if too damaged. Don’t risk your feet without steel toe fix.
Insole and Lining Repair
Boot linings that are torn or worn extra smooth need the skills of a pro to neatly mend. Same for insoles with no arch support left or separated from the welt. They have industrial sewing machines to re-stitch linings and special adhesives to re-bond insoles.
Don’t try to glue down insoles yourself—it won’t last. Let the experts handle it.
Customization
Beyond repairs, boot makers can customize boots with special features like adding cushion pads, traction pads, metatarsal guards, custom orthotics, extra insulation and more. They have the expertise to modify boots to meet your needs.
Find a High Quality Shop
Take boots into a dedicated boot repair shop versus a random cobbler. Ask around for recommendations of craftsmen experienced with work boots specifically. Review their repair portfolio and ask about the durability of their resoling and repairs.
Established shops with a bootmaker on staff often provide the best service. Be picky to ensure lasting fixes.
Determine Cost Effectiveness
Consider the repair cost relative to just replacing your boots. Major resoling jobs can run $60-80 for quality work. Compare that to the cost of new boots and whether replacement makes more sense.
If boots are otherwise comfy with minimal upper wear, repairs are usually worthwhile to extend their lifespan vs. breaking in brand new boots.
Prioritize functionality over cosmetics when evaluating repairs. The goal is safe, supportive boots—not runway looks.
Do your wallet and feet a favor by making quality work boot repairs when feasible. For major structural and sole issues, leave it to the craftsmen. They have the know-how to restore your boots’ reliability so you can keep working with peace of mind.
Extending the Life of Your Favorite Boots
Finding that perfect pair of work boots that have just the right fit and feel can make you want to wear them forever. While it’s impossible to make boots last indefinitely, there are things you can do to care for them properly and extend their lifespan as long as possible.
Break Them In Slowly
Take the time upfront to properly break in new boots before heavy use. Wear them for short periods at first, using a boot stretcher spray at night to gently loosen tight spots. Build up to longer wears over 2-3 weeks until they feel molded to your feet.
Rushing this process can over-stress materials and stitching early on. Patience pays off with boots that feel custom-fit just for you.
Rotate Regularly
Wearing the same boots daily wears them out quicker by not allowing materials to rest and dry out fully between wears. Make it a habit to rotate between at least 2-3 pairs and allow boots to air out for 24 hours before the next wear.
Alternating boots significantly reduces repeat stress on the same flex points and seams each day. Your boots last longer with regular breaks.
Use Cedar Shoe Trees
Placing cedar shoe trees inside boots when not being worn preserves their structure and absorbs moisture. Cedar’s natural aroma repels odors too. The trees keep boots upright to prevent creasing and wrinkling of materials that can lead to cracks.
Sagging, crumpled boots wear out faster. Shoe trees are an inexpensive way to make your footwear investment last.
Clean and Condition
Don’t let dirt, grime and salt buildup deteriorate leather and materials prematurely. Use a dedicated boot brush with stiff bristles to regularly remove mud and debris. Clean insides periodically with mild soap and water.
Keep leather supple and protected with occasional conditioner. For suede boots, revive the nap with a suede brush. Proper cleansing keeps them looking like new longer.
Weatherproof
Treating boots with a weatherproofing spray repels water and stains to prevent damage. Silicone-based sprays also condition leather. Reapply every few months as needed, letting the spray fully dry before wearing.
Waterproofed boots maintain their integrity better when faced with the elements daily.
Heel and Sole Upkeep
Inspect heel and soles routinely for wear. At first signs of thin tread or loose heels, take boots in for repairs. Re-soling and re-heeling restores traction and extends boot life vs. waiting until irreparable.
Carry replacement heels/taps to swap out immediately when current ones wear smooth.
Re-Lace
Don’t wait for laces to snap to replace them. At first signs of fraying or damage, install new quality laces designed for work boots. Look for reinforced tips and durable fabrics that withstand abrasion.
Proper lacing reduces strain on eyelets too. Snug midfoot lacing secures boots firmly to feet and prevents excess movement that wears materials faster.
Use a Dryer
Wet boots lead to deterioration of stitching, warping of leather and interior odor. Extend boot life by placing them on a boot dryer after each shift. The dry circulating air speeds evaporation so they dry fully overnight.
Rotating boots on the dryer ensures both toe and heel areas dry out completely before the next wear.
Add a Toe Guard
Toes take a beating and are often the first spot to wear out. Adding a rubber toe guard provides an extra shield against scuffs, abrasion and contact hazards.
Look for full coverage caps that adhere securely. Replace immediately if they start peeling or come loose.
Store Properly
Don’t toss boots in a hot shed or garage between shifts. Keep them stored upright on boot trees in a cool, dry area out of direct sunlight. Avoid attics or basements prone to moisture.
Heat and humidity can degrade leather and materials quickly. The right storage environment keeps boots fresh.
With vigilant care and maintenance, you can keep favorite boots going strong for years. Take time for cleaning, conditioning and repairs along the way. Your feet will thank you for properly preserving that custom fit and feel you love.
Conclusion: Rubber Patches for Reliable Boot Repair
When wear and tear inevitably takes its toll on your trusted work boots, don’t despair. With the right patching techniques and materials, you can often restore them to working order. Sturdy rubber patches properly adhered can cover holes and damaged spots for a seamless fix. They provide a flexible and waterproof barrier that conforms to the boot shape and stays securely bonded.
Take care to clean and prepare the damaged area thoroughly before applying patches. Seal the edges and use pressure to smooth patches firmly in place. Blend edges gently for an invisible repair. With occasional re-patching when necessary, boots can be kept going strong for years before needing full sole or upper replacement.
While DIY patches work for minor fixes, knowing when to seek professional help ensures major structural issues are properly addressed for safety and performance. With a quality rubber patch kit on hand, you’ll be prepared to make lasting fixes and keep favorite boots on your feet comfortably.