Looking to Buy a Warehouse in Baltimore This Year. Here are 15 Key Things to ConsiderLooking to Buy a Warehouse in Baltimore This Year. Here are 15 Key Things to Consider
Location – What part of Baltimore has available warehouses for sale?
If you’re considering purchasing a warehouse in Charm City this year, there are several key factors to take into account before signing on the dotted line. With its strategic location on the East Coast and proximity to major highways, railroads and ports, Baltimore has long been an attractive market for industrial and logistics companies. However, not all areas of the city offer the same amenities and opportunities. Here are 15 vital considerations when looking to buy a warehouse in Baltimore.
1. Transportation access
One of the most important criteria is proximity to major transportation infrastructure. Being near interstate highways like I-95 allows for easy distribution of goods by truck throughout the Mid-Atlantic region and beyond. Close access to rail lines and marine ports also facilitates shipping to customers across the country and overseas. Areas like Locust Point, Fairfield and the Point Breeze/Broening Highway corridor offer direct connections to these transportation networks.
2. Labor pool
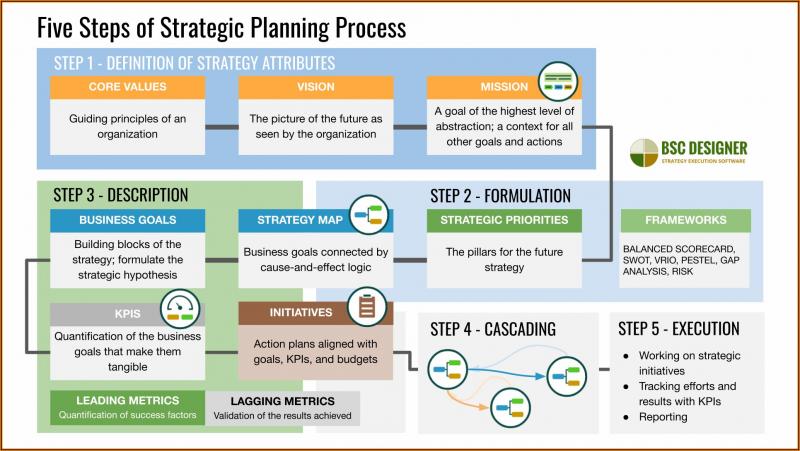
Another key factor is having access to a qualified workforce. Selecting a location near densely populated neighborhoods ensures a robust labor pool to recruit from. Areas like Southwest Baltimore, Dundalk and Essex offer an abundant supply of potential employees with varying skill sets and education levels.
3. Utility infrastructure
Warehouses use significant amounts of electricity, gas, water and sewer services. Ensuring adequate utility infrastructure exists in a location you’re considering can avoid headaches down the road. Target areas already zoned for industrial use that offer the power, water and sewer capacity needed to operate a warehouse facility.
4. Room for expansion
Think about future growth needs and seek out properties where you can expand operations over time. Look for vacant adjacent land or buildings that provide opportunities to add on as your business scales up. Locations on the outskirts of the city or in suburbs like Halethorpe and Elkridge often provide more expansion possibilities.
5. Zoning regulations
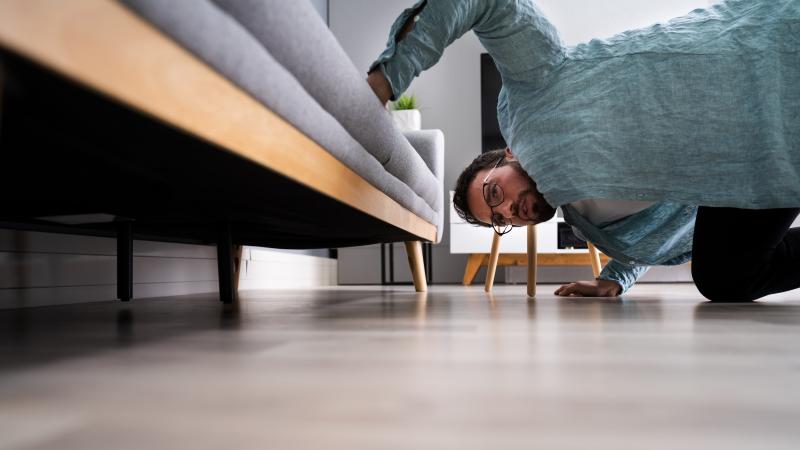
Carefully research the zoning classification and land use regulations for any property you’re evaluating. You’ll want to ensure the area is actually approved for warehousing, distribution or light industrial use. The zoning should specifically permit the activities your business will engage in to avoid issues with non-conforming uses down the line.
6. Purchase or lease options
Determine whether you want buy a warehouse outright or lease initially. Purchasing provides long-term stability and equity, while leasing offers more flexibility as you test the waters. Explore both purchase prices and lease rates in your target locations to understand your options.
7. Loading docks
Having adequate loading bays is imperative for efficiently receiving and shipping your products via truck. Look for existing buildings with multiple dock doors and high ceilings to accommodate trailer access. If constructing new, plan enough space in your dock design to handle increased traffic as operations grow.
8. Clear ceiling height
- Interstate highways (e.g., I-95)
- Rail lines
- Marine ports
How does this benefit your operations? Proximity to these networks facilitates efficient distribution of goods throughout the Mid-Atlantic region and beyond, potentially reducing shipping times and costs.
Labor Pool: Tapping into Baltimore’s Workforce
The success of your warehouse operation hinges on access to a qualified workforce. Which areas of Baltimore offer the best labor pool? Southwest Baltimore, Dundalk, and Essex stand out as prime locations. These densely populated neighborhoods provide a diverse range of potential employees with varying skill sets and education levels.
Infrastructure and Utilities: Powering Your Warehouse Operations
The backbone of any efficient warehouse is its utility infrastructure. How can you ensure your chosen location meets your operational needs?
Utility Capacity: Meeting High Demands
Warehouses are notorious for their high utility consumption. What should you look for in terms of utility infrastructure?
- Adequate electrical capacity (preferably 480-volt, 3-phase power)
- Sufficient water supply
- Robust sewer systems
- Natural gas availability (if needed)
Target areas already zoned for industrial use, as these are more likely to have the necessary utility infrastructure in place.
IT Infrastructure: Connecting Your Warehouse to the Digital World
In today’s digital age, a warehouse’s IT capabilities are as crucial as its physical infrastructure. What IT elements should you consider?
- High-speed internet connectivity
- Capacity for Warehouse Management Systems (WMS)
- Support for barcode scanners and RFID technology
- Robust wireless networks
- VoIP phone systems
Ensure your chosen location either has these capabilities or can easily be upgraded to support your IT needs.
Future-Proofing Your Investment: Room for Expansion
When investing in a warehouse, it’s crucial to think beyond your current needs. How can you ensure your chosen location allows for future growth?
Expansion Possibilities: Looking Beyond Today
Consider locations that offer:
- Adjacent vacant land
- Nearby buildings available for acquisition
- Zoning that allows for future expansion
Areas on the outskirts of Baltimore or in suburbs like Halethorpe and Elkridge often provide more expansion possibilities. How might this impact your long-term business strategy?
Regulatory Landscape: Navigating Zoning and Land Use
Understanding the regulatory environment is crucial when investing in a warehouse. What zoning considerations should be on your radar?
Zoning Classifications: Ensuring Compliance
Before finalizing any warehouse purchase, thoroughly research the property’s zoning classification and land use regulations. What should you look for?
- Approval for warehousing and distribution activities
- Permissions for light industrial use
- Compatibility with your specific business operations
By ensuring your intended use aligns with local zoning regulations, you can avoid costly non-conforming use issues in the future.
Financial Considerations: Purchase vs. Lease
When entering the Baltimore warehouse market, you’ll need to decide whether to buy or lease. What factors should influence this decision?
Ownership Benefits: Building Long-term Equity
Purchasing a warehouse outright offers several advantages:
- Long-term stability
- Building equity over time
- Greater control over the property
- Potential tax benefits
However, it also requires a significant upfront investment and ongoing maintenance responsibilities.
Leasing Flexibility: Testing the Waters
Leasing a warehouse can be an attractive option, particularly for businesses new to the Baltimore market. Benefits include:
- Lower initial costs
- Flexibility to relocate as needs change
- Reduced maintenance responsibilities
- Opportunity to test different locations
Compare purchase prices and lease rates in your target locations to make an informed decision based on your financial situation and long-term goals.
Operational Efficiency: Key Warehouse Features
The physical features of a warehouse play a crucial role in its operational efficiency. What elements should you prioritize?
Loading Docks: The Gateway to Your Warehouse
Efficient loading and unloading are essential for smooth warehouse operations. What should you look for in terms of loading docks?
- Multiple dock doors to handle simultaneous shipments
- High ceilings to accommodate trailer access
- Levelers and seals for weather protection
- Ample maneuvering space for trucks
If constructing a new facility, plan for future growth by including extra dock space in your design.
Clear Ceiling Height: Maximizing Vertical Space
High ceilings are a valuable asset in warehouse operations. Why? They allow for:
- Efficient vertical storage
- Use of taller racking systems
- Easier maneuverability for forklifts and other equipment
Look for clear heights of at least 24 feet to optimize storage density and operational efficiency.
Environmental Control: Protecting Your Inventory
Depending on your inventory, environmental control may be crucial. What factors should you consider?
Climate Control Systems: Preserving Product Integrity
For businesses dealing with temperature-sensitive goods like food or pharmaceuticals, climate control is non-negotiable. What should you look for?
- Existing HVAC systems capable of maintaining specific temperature ranges
- Humidity control capabilities
- Zoned climate control for different product requirements
- Energy-efficient systems to manage operating costs
If acquiring a bare shell building, ensure there’s ample space and infrastructure to install a robust climate control system cost-effectively.
Security Measures: Safeguarding Your Assets
Protecting your inventory, equipment, and data is paramount in warehouse operations. What security features should you prioritize?
Physical Security: Creating a Secure Perimeter
Look for warehouses that offer or have the potential to implement:
- Perimeter fencing with controlled access points
- Security lighting around the building and parking areas
- Secure loading dock doors with locking mechanisms
- Reinforced entry points to deter break-ins
Technological Security: Leveraging Modern Solutions
In addition to physical barriers, modern warehouses benefit from technological security measures such as:
- CCTV camera systems with remote monitoring capabilities
- Access control systems using key cards or biometrics
- Alarm systems with direct links to local law enforcement
- Cybersecurity measures to protect digital assets and data
When evaluating a potential warehouse, assess the existing security infrastructure and factor in the costs of any necessary upgrades.
Employee Amenities: Creating a Productive Work Environment
While the primary focus of a warehouse is storage and distribution, don’t overlook the importance of employee amenities. How can these features impact your operations?
Office Spaces: Supporting Administrative Functions
Look for warehouses that offer:
- Dedicated office areas for management and administrative staff
- Meeting rooms for team collaborations and client visits
- Adequate parking for employees and visitors
Employee Comfort: Boosting Morale and Productivity
Consider warehouses that provide or have space for:
- Break rooms or cafeterias for meal times
- Locker rooms and restroom facilities
- Outdoor areas for fresh air breaks
- Training rooms for ongoing skill development
Investing in employee amenities can lead to increased job satisfaction, reduced turnover, and improved overall productivity.
Future-Proofing Your Warehouse: Embracing Technological Advancements
The warehouse industry is rapidly evolving with new technologies. How can you ensure your Baltimore warehouse investment remains competitive in the years to come?
Automation Readiness: Preparing for the Future of Logistics
Consider warehouses that can accommodate or be easily modified for:
- Automated storage and retrieval systems (AS/RS)
- Robotic picking and packing solutions
- Automated guided vehicles (AGVs) for internal transport
- IoT sensors for inventory tracking and environmental monitoring
While you may not implement these technologies immediately, choosing a warehouse with the potential for automation can future-proof your investment.
Sustainable Design: Meeting Environmental Standards
As environmental regulations tighten and consumers demand more sustainable practices, consider warehouses that offer or can be upgraded with:
- Energy-efficient lighting systems (e.g., LED fixtures with motion sensors)
- Solar panel-ready roofing for potential renewable energy integration
- Water conservation features like rainwater harvesting systems
- Electric vehicle charging stations for company vehicles and employee use
Investing in a sustainable warehouse not only reduces operating costs but also enhances your company’s environmental profile.
Local Community Impact: Being a Good Corporate Neighbor
When investing in a Baltimore warehouse, it’s crucial to consider your impact on the local community. How can you ensure your warehouse operation contributes positively to the area?
Job Creation: Boosting Local Employment
Your warehouse can be a significant source of employment for the local community. Consider:
- Partnering with local job training programs
- Offering apprenticeships or internships for area students
- Prioritizing local hiring for various skill levels
Community Engagement: Building Strong Relationships
Engage with the local community by:
- Participating in local business associations
- Supporting community events and initiatives
- Implementing noise reduction measures to minimize disruption
- Maintaining the aesthetic appeal of your property
By being a responsible corporate citizen, you can foster goodwill and potentially smooth the way for future expansion or zoning requests.
Legal and Financial Due Diligence: Protecting Your Investment
Before finalizing your warehouse purchase in Baltimore, it’s crucial to conduct thorough legal and financial due diligence. What key areas should you focus on?
Title Search and Insurance: Ensuring Clear Ownership
Conduct a comprehensive title search to:
- Verify the seller’s right to transfer the property
- Identify any existing liens or encumbrances
- Uncover any easements or restrictive covenants
Invest in title insurance to protect against unforeseen title issues that may arise after purchase.
Environmental Assessment: Mitigating Potential Liabilities
Given Baltimore’s industrial history, it’s crucial to conduct thorough environmental assessments. This should include:
- Phase I Environmental Site Assessment to identify potential contamination
- If necessary, a Phase II assessment for soil and groundwater testing
- Review of historical property uses and nearby industrial activities
Understanding the environmental status of the property can help you avoid costly remediation efforts and potential legal liabilities in the future.
Financial Analysis: Ensuring a Sound Investment
Before committing to a warehouse purchase, conduct a thorough financial analysis, including:
- Comparative market analysis of similar properties in the area
- Projected operating costs and potential revenue streams
- Return on investment calculations
- Cash flow projections considering various occupancy scenarios
Engaging with local real estate professionals and financial advisors can provide valuable insights into the Baltimore warehouse market and help ensure your investment aligns with your long-term financial goals.
Navigating Baltimore’s Unique Warehouse Landscape
Baltimore’s rich industrial history and strategic location make it a unique market for warehouse investments. How can you leverage the city’s specific advantages?
Port of Baltimore: Capitalizing on Maritime Trade
The Port of Baltimore is a major asset for warehouse operators. Consider how proximity to the port could benefit your operations:
- Faster access to imported goods
- Reduced transportation costs for exports
- Potential for specialized services like cold storage for perishables
- Opportunities in value-added services for port-related businesses
Urban Logistics: Meeting the Demands of City Dwellers
As e-commerce continues to grow, urban warehouses are becoming increasingly valuable. How can you tap into this trend in Baltimore?
- Look for smaller, strategically located warehouses for last-mile delivery
- Consider multi-story warehouses in densely populated areas
- Explore mixed-use developments that combine warehousing with other commercial spaces
By understanding and leveraging Baltimore’s unique characteristics, you can position your warehouse investment for long-term success in this dynamic market.
Location – What part of Baltimore has available warehouses for sale?
If you’re considering purchasing a warehouse in Charm City this year, there are several key factors to take into account before signing on the dotted line. With its strategic location on the East Coast and proximity to major highways, railroads and ports, Baltimore has long been an attractive market for industrial and logistics companies. However, not all areas of the city offer the same amenities and opportunities. Here are 15 vital considerations when looking to buy a warehouse in Baltimore.
1. Transportation access
One of the most important criteria is proximity to major transportation infrastructure. Being near interstate highways like I-95 allows for easy distribution of goods by truck throughout the Mid-Atlantic region and beyond. Close access to rail lines and marine ports also facilitates shipping to customers across the country and overseas. Areas like Locust Point, Fairfield and the Point Breeze/Broening Highway corridor offer direct connections to these transportation networks.
2. Labor pool
Another key factor is having access to a qualified workforce. Selecting a location near densely populated neighborhoods ensures a robust labor pool to recruit from. Areas like Southwest Baltimore, Dundalk and Essex offer an abundant supply of potential employees with varying skill sets and education levels.
3. Utility infrastructure
Warehouses use significant amounts of electricity, gas, water and sewer services. Ensuring adequate utility infrastructure exists in a location you’re considering can avoid headaches down the road. Target areas already zoned for industrial use that offer the power, water and sewer capacity needed to operate a warehouse facility.
4. Room for expansion
Think about future growth needs and seek out properties where you can expand operations over time. Look for vacant adjacent land or buildings that provide opportunities to add on as your business scales up. Locations on the outskirts of the city or in suburbs like Halethorpe and Elkridge often provide more expansion possibilities.
5. Zoning regulations
Carefully research the zoning classification and land use regulations for any property you’re evaluating. You’ll want to ensure the area is actually approved for warehousing, distribution or light industrial use. The zoning should specifically permit the activities your business will engage in to avoid issues with non-conforming uses down the line.
6. Purchase or lease options
Determine whether you want buy a warehouse outright or lease initially. Purchasing provides long-term stability and equity, while leasing offers more flexibility as you test the waters. Explore both purchase prices and lease rates in your target locations to understand your options.
7. Loading docks
Having adequate loading bays is imperative for efficiently receiving and shipping your products via truck. Look for existing buildings with multiple dock doors and high ceilings to accommodate trailer access. If constructing new, plan enough space in your dock design to handle increased traffic as operations grow.
8. Clear ceiling height
In addition to dock doors, sufficient clear ceiling height allows for easy stacking and retrieval of inventory by forklift or other equipment. Look for clear heights of at least 24 feet for optimum storage density and operational efficiency.
9. Power capabilities
From conveyors to lifts to lighting, warehouses use substantial electricity. Evaluate if the facility’s electrical system provides enough power capacity for all your equipment needs. Look for 480-volt, 3-phase power supplies with ample circuit breaker space for additions.
10. Climate control
Some types of inventory, like food or pharmaceuticals, require temperature and/or humidity control for proper storage. If climate control is needed, seek out buildings with existing HVAC systems or ample space to install your own system cost effectively.
11. Security
Protecting your valuable inventory, equipment and data is paramount. Look for features like perimeter fencing, secure access doors, camera systems and on-site security personnel. Have a plan for implementing security measures if acquiring a bare shell building.
12. Office/employee amenities
In addition to the warehouse itself, you’ll need office space for staff and ideally some employee amenities like a break room or cafeteria. Seek out properties with existing office build-outs or enough vacant space to create the facilities you need.
13. IT infrastructure
Modern warehouses rely heavily on IT systems like WMS (warehouse management systems) software, barcode scanners, wireless networks and VoIP phone systems. Ensure the location you choose either has capable IT infrastructure in place or the ability to install what your operation requires.
14. Access to highways and roads
Convenient access to major highways, arteries and truck routes makes transportation logistics much simpler. Prioritize locations near I-95, I-70, Route 295 and other main transportation corridors around Baltimore.
15. Financing options
Whether purchasing a property outright or constructing a new warehouse, understand your financing options. Talk to banks and lenders to get pre-approved for loans and explore economic development incentives from state and local governments.
With careful evaluation across these key factors, you can zero in on the ideal Baltimore location for your organization’s warehouse needs. Partnering with an experienced commercial real estate broker knowledgeable about Baltimore’s industrial market can help streamline your search. They can pinpoint listings meeting your criteria and provide objective insight on pros and cons of different areas and properties. Investing the time upfront to make the right warehouse choice will pay dividends for years down the road.
If you’re in the market for a warehouse in Charm City, you’ve got plenty of options, but the choice can be overwhelming. Baltimore’s industrial real estate market is active, with hundreds of facilities for sale or lease at any given time. Before you start touring properties, get clear on your needs. Buying a warehouse is a major investment, so make sure yours will truly support your business now and in the years ahead.
To find your ideal Baltimore warehouse, consider these 15 key factors:
Size – How much square footage do you need? Consider inventory needs.
Crunching the numbers on size requirements takes some strategic thinking. Of course, you want enough space to comfortably accommodate current inventory, operations, and staff. But the smartest investment considers growth projections down the road. Overbuying on square footage ties up precious capital. Underbuying leads to costly relocations. Right-sizing means thinking through:
- What’s your inventory footprint today? What about in 3-5 years?
- How much area for receiving, shipping, production lines, and other operations?
- Office needs – both for people and equipment?
- Any special accommodations like high ceilings for racking systems?
Precisely defining needs makes it easier to zero in on the sweet spot for square footage.
Location – What’s most convenient for you?
Baltimore has a diversity of industrial neighborhoods, each with its own flair. Make sure you choose an area aligned with your priorities, such as:
- Proximity – Close to suppliers, clients, airport/ports?
- Access – Easy highway access for truck routes?
- Zoning – Does the area permit your type of business?
- Amenities – Dining/shopping nearby for employees?
- Environment – Urban vibe or suburban campus?
Map out your frequent destinations and preferred surroundings. This makes it easier to pinpoint target submarkets.
Building Class – What condition space do you need?
Baltimore’s industrial buildings range from older, minimalist shells to new construction with all the modern bells and whistles. The class you choose significantly impacts cost. Consider:
- Class A: Recently built; state-of-the-art systems; premium finishes
- Class B: 1980s-1990s construction; functional/good condition
- Class C: Older building; basic construction; may need renovations
Class A commands the highest rents but offers the newest systems. Fixer-uppers can be a shrewd value for budget-conscious companies willing to update gradually over time.
Loading – What are your dock and drive-in needs?
Loading docks are essential for daily warehouse operations. Determine:
- Number of docks needed for receiving/shipping
- Drive-in bays for additional access
- Dock door dimensions – Does your largest truck fit?
- Dock levelers/seals for smooth loading?
- Space around docks for staging and maneuvering
Having ample, properly-equipped docks prevents bottlenecks in your workflow.
Power – What type of supply suits your use?
From lighting to machinery, warehouses eat up electricity. Evaluate if the area’s standard power supply meets your needs or if upgraded service is required. Options include:
- 208/120V: Typical power for small equipment/appliances
- 480/277V: For running heavy machinery or industrial equipment
- 3-phase: For larger equipment needs, conveyors, motors
- Higher amperage: More power capacity for specialized operations
Any anticipated spikes in usage should be factored in. Insufficient power leads to tripped breakers and downtime.
Design – What layout options work for your processes?
Baltimore warehouses range from wide-open freezers to intricate manufacturing ops. Make sure the design accommodates your needs with:
- Clear height for racking/machinery
- Column spacing for optimizing storage cubes
- Adjacent office space or room for expansion
- Divisible space to accommodate future tenants
- Temperature-controlled areas as needed
Thoroughly planning workflow and layout avoids productivity-zapping bottlenecks.
Safety – What fire prevention and security features are needed?
Warehouse risks span building systems, human error, and outside threats. Protect your people, goods, and business continuity through features like:
- Sprinklers & fire alarms
- Smoke/heat sensors
- Security systems
- Backup generators
- Adequate emergency exits
Upgrading missing safety essentials improves protection and can reduce insurance premiums.
Parking – Is there sufficient room for workers/visitors/trucks?
Inadequate parking bogs down operations and frustrates everyone trying to get in and out. Evaluate:
- Employee parking needs
- Visitor/customer parking
- Truck maneuvering/queuing space
- Overflow parking potential
- Secure, designated parking areas
Proper parking clearance minimizes bottlenecks and dangers when navigating the facility.
Dock & Yard – Does the configuration support efficient flow?
The warehouse doesn’t operate in isolation – docks and yards enable the flow of goods in and out. Look for:
- Logical door placement for loading workflow
- Sufficient trailer/container parking near docks
- Adequate room for trucks to maneuver
- Clear drive lanes around the perimeter
Poor dock and yard layouts bog down operations and create hazards.
Construction – What building features are needed?
Baltimore’s industrial building stock runs the gamut from older functionally obsolete to new Class A structures. Key considerations:
- Building age, condition and anticipated maintenance/upgrade costs
- Construction method – precast concrete, tilt-up, steel
- Façade and roof condition
- Office buildout and common area finishes
Prioritize must-have structural and system fundamentals over cosmetic finishes.
Systems – What mechanical, electric & plumbing shape up best?
Building systems keep warehouse operations humming along. Assess:
- Heating and cooling capacity – is it right-sized?
- Lighting suits the use
- Restrooms sufficient for occupancy
- Clear ceilings and stable foundations
- Reliable roof and plumbing
Prioritize upgrades that resolve red flags and safety issues.
Accessibility – Is the facility ADA compliant?
Many older Baltimore warehouses pre-date ADA requirements. Upgrading for accessibility may be needed for:
- Parking, ramps, doorways
- Bathrooms and common areas
- Signage, alarms, controls placed within reach
Ensuring ADA compliance shows employees and customers they are valued.
Sustainability – Are green features a priority?
Sustainable warehouses use less energy, lower overhead costs, and promote corporate citizenship. Options include:
- Energy efficient T5/LED lighting
- Solar ready roof space
- Low-flow plumbing fixtures
- Added insulation
- Thermostat setbacks and smart sensors
Even modest green upgrades significantly bolster sustainability.
Incentives – Are there opportunities for subsidies or tax breaks?
Federal, state, and local programs provide incentives for investing in disadvantaged areas or upgrading old facilities. These include:
- Location-based tax credits
- Energy efficiency rebates
- Grants for new job creation
- Financing assistance
Tapping available incentives cushions costs for buyers willing to do the legwork.
Weighing all these factors prepares you to zero in on the ideal Baltimore warehouse for your needs. Balancingrequirements and cost helps strike the sweet spot. With proper due diligence, your new facility will effectively support operations for years to come.
If you’re searching for warehouse space in Charm City, ya got options galore. But choosin’ the right digs is no cakewalk, hon. Buying a warehouse is major dough, so make darn sure yours suits your biz now and down the road, ya hear?
To find your dream Bawlmer warehouse, give these 15 need-to-knows a think:
Zoning – Is the property zoned for commercial/industrial use?
Zoning rules dictate what you can and can’t do on a property. Make sure your planned use – manufacturing, distribution, etc – is permitted. If not, a rezoning fight can torpedo the deal. Do your homework to ensure the zone works for:
- Your operations like manufacturing, storage, offices
- Shift work, late hours, truck traffic
- Hazardous materials, noise, odors
- Retail if you need a showroom
Improper zoning spells trouble. Don’t get stuck with a dud.
Size – How much square footage will cut the mustard?
Crunching the numbers on space needs takes strategy, see? Of course you want room to swing a cat for inventory, ops, the whole nine. But smart money looks down the pike. Too much space ties up moolah. Too little means pricy moves. Right-sizing is about:
- Today’s inventory bebop. And 2, 3 years out?
- Operations – shipping, receiving, the works
- Office stuff and equipment
- High ceilings? Other bells and whistles?
Defining needs helps target the square footage goldilocks zone, see?
Location – What’s most convenient for you?
Bawlmer’s got industrial pockets with their own vibe. Choose a spot aligned with your groove:
- Close to suppliers, clients, ports
- Easy highway access for trucks
- Zoning permits your scenes
- Grub and shops for employees
- Urban action or suburban chill?
Map your hangouts and digs to pinpoint target ‘hoods, ya dig?
Building Class – What condition space suits your scene?
Warehouses here range from barebones to new with all the fixins. Class impacts cost, so case it:
- Class A: New build; primo systems; swanky finishes
- Class B: ’80s-’90s; decent shape
- Class C: Older; basic; might need renovation
Class A demands top rental scratch but it’s new jack. Fixer-uppers can be a value for bargain hunters willin’ to update over time.
Loading – What are your dock and drive-in needs?
Loading docks are clutch for daily ops. Figure:
- Docks needed for shipping/receiving?
- Drive-ins for extra access
- Big enough doors for your trucks?
- Dock levelers/seals for smooth loadin’?
- Room to bob and weave around the docks
Well-equipped docks avoid bottlenecks in your flows.
…Article Continues…
…Article Continues…
Condition – What repairs or upgrades will the building need?
Baltimore’s warehouses range from turnkey modern to major fixer-uppers. Assess current condition and likely future costs for:
- Roof, walls, foundation – any issues?
- Electrical, lighting, restrooms functional?
- HVAC adequacy and age of systems
- Dock equipment condition – levelers, seals etc.
- Cleanup, paint, carpeting needs?
- Sprinklers, security and safety features
Cosmetic fixes are lower priority than structural and mechanical necessities. But don’t underestimate “soft” costs like cleanup and paint when budgeting your total investment.
Layout – Does the floorplan align with your workflow?
An inefficient layout cripples productivity. Ensure the space accommodates your needs for:
- Receiving and shipping flow
- Equipment positioning
- Assembly or work zones
- Offices, breakrooms, bathrooms
- Storage layout – racks, aisles, clear heights
Test-drive the layout mentally from delivery to dispatch to pinpoint any sticking points before move-in.
IT Infrastructure – Is connectivity up to speed?
Today’s data-driven operations need robust IT infrastructure. Assess:
- Internet/network availability, speed and reliability
- WiFi coverage for offices, mobile devices
- Access to fiber optic connections
- Ability to install needed wiring, servers etc.
Upgrading connectivity could be a “must-have” for maximizing warehouse technology capabilities.
Ceiling Clearance – Is there enough overhead room?
Lofty warehouses feel open and airy but that height serves a purpose. Verify you have ample clearance for:
- Racking systems
- Mezzanines
- Cranes, conveyors or other overhead equipment
- Lighting, ductwork, piping, sprinklers
- Truck trailer heights
Too little overhead clearance crimps storage density and operations.
Loading Docks – Are there enough doors and spaces?
Loading docks are a warehouse’s lifeblood. Make sure the dock count and dimensions fit needs for:
- Number of shipping/receiving bays required
- Space for trucks to park adjacent to docks
- Adequate drive lanes and turning radii
- Room for staging loaded trailers
Expanding docks later is costly – better to size up correctly from the start.
…Article Continues…
…Article Continues…
Accessibility – Is it easy to get to for employees and customers?
A warehouse’s location impacts how conveniently it can be accessed. Prioritize facilities close to:
- Highways, interstates, rail lines
- Airports, shipping ports
- Public transit for employees
- Amenities like eateries, gas stations
Ideally, choose a site near major truck routes and population hubs to minimize commute times.
Parking – Is there enough room for workers and visitors?
Inadequate parking causes daily headaches. Analyze:
- Spaces required for employees, customers
- Room for secure trailer parking
- Accommodations for oversize vehicles
- Handicap accessible stalls
- Scope for future expansion
Proper parking clearance prevents bottlenecks and safety issues.
Compliance – Does it meet codes and regulations?
Pre-purchase due diligence should verify:
- Current fire, building, occupancy certificates
- Zoned properly for your use
- ADA compliant access and facilities
- Environmental condition of site
- Complies with labor laws, regulations
Violations can mean unexpected headaches and costs down the road.
Carefully weighing all these factors prepares you to identify the perfect Baltimore warehouse for your needs. Finding the ideal balance of requirements and cost helps ensure your new facility effectively supports operations for years to come.
If you’re looking to purchase a warehouse in Baltimore this year, there are several important factors to take into account before making this major investment. With the right research and planning, you can find the ideal warehouse space to meet your business’s current and future needs.
Parking – Is there enough parking for staff and visitors?
One of the top considerations is parking availability. Depending on your business, you may need parking for dozens or even hundreds of employees, plus additional spaces for visitors and customers. Evaluate both the number of spaces and parking lot configuration. Make sure there is sufficient room for easy circulation and maneuvering of vehicles. The parking should also be convenient and proximal to the warehouse entrance(s). If the existing parking is inadequate, find out if additional parking can be added onsite or nearby. The costs of leasing, purchasing or paving more parking area may impact the overall viability and expenses of purchasing the warehouse.
Loading Docks – What is the dock configuration?
The number, dimensions, door types, and overall layout of loading docks will have a significant impact on warehouse operations. Make sure there are enough docks with the right door sizes and levels to handle anticipated shipping and receiving volume. The ideal configuration allows for efficient material flow in and out of the facility. Having spacious room around the loading area also allows for easier maneuvering of lift trucks and other material handling equipment. If the property lacks necessary shipping/receiving infrastructure, find out if docks can be expanded or added.
Ceiling Height – Is there sufficient clearance?
Interior clearance is another key consideration, especially for facilities utilizing vertical space for pallet racks or other storage systems. While requirements vary by industry and storage methods, higher ceiling heights allow for more optimized space usage. Look at the clearance not just at the peaks but also beams, lighting, HVAC, sprinklers and other potential obstructions. Ceiling height may also impact what type of racking can be installed. Verifying the existing ceiling height and determining if the height can be economically increased will inform what storage density is possible in the space.
Power – Is there access to the needed utility services?
Evaluate whether the warehouse’s electrical system can supply the power demands for your equipment and operations. This may require bringing in specialized contractors to inspect the premises. You’ll want to understand the number and voltage of panels, amperages, outlets, lighting circuits and more. Make sure the power supply is sufficient, reliable and redundant enough to handle sensitive electronics, heavy machinery, charging stations and the overall energy loads. Also look at needs for other utilities like gas, water, sewer and telecommunications.
Location – Is the site optimal for business operations?
Carefully consider the warehouse location relative to your supply chain, logistics networks, customer base and labor pool. A site close to key transportation infrastructure like interstates, rail lines, ports and airports can significantly improve operational efficiency. However, proximity also brings potential downsides like noise, traffic congestion and environmental impacts. Look at the neighboring properties and be mindful of current zoning as well as possible future developments. Comprehensive location analysis will ensure the site aligns with business objectives.
Condition – What is the overall state of the building?
While some buyers may look to purchase fixer-uppers, be wary of facilities requiring excessive repairs or renovations. Inspect both the exterior and interior to assess roofing, HVAC, plumbing, electrical, sprinklers, structural soundness and more. Look for signs of leaks, damage, pest infestations and other issues needing remediation. Also consider aesthetic elements like cleanliness, odors, and overall appeal. Evaluate compliance with fire, safety and accessibility codes as well. Understanding the true condition will inform renovation budgets and timelines.
Layout – Does the floorplan optimize workflow?
An efficient warehouse layout supports smooth product flow and operations. Review how the space is currently divided into receiving, storage, picking, packing, shipping and other functional areas. Identify any pinch points or bottlenecks that hinder material movement and replenishment. Also look at openness, aisle widths and clear heights that affect maneuverability. A poor existing layout may necessitate significant and costly reconfigurations. But the layout also presents opportunities to customize the space for optimal material handling.
Construction – What is the building envelope and structure?
Carefully examine the warehouse’s construction including age, building materials, insulation, windows, and more. This will impact durability as well as heating and cooling costs over time. Also look at the foundation and weight loading capacity to ensure it can hold inventory loads. Ideally the structural elements require minimal maintenance while providing safety and security. Understand any needs to reinforce the building envelope or replace aging materials like roofs. Also ask about any building code or occupancy changes.
Safety – Does the facility promote worker wellbeing?
Any warehouse acquisition should prioritize worker health and safety. Review the fire prevention, suppression, and alarm systems. Ensure adequate exits, emergency lighting, signage, and fire extinguishers. Also look at slip/trip/fall hazards in transition areas and see if flooring meets coefficient of friction requirements. Evaluate how warehouse racking, machinery, and lifting equipment is installed, guarded and maintained. A safe, compliant facility helps mitigate regulatory risks and promotes productivity.
Technology – What material handling and tracking systems are in place?
Modern warehouses utilize technology for inventory management, order fulfillment, shipping/receiving, and automation. Assess existing warehouse management systems, barcode scanning, radio frequency devices, sensors, and more. Look at how technology is integrated with material handling equipment like conveyors, sorters, pick-to-light systems, and automated storage and retrieval systems. If upgrading technology, factor in IT infrastructure as well as employee training needs.
By taking these key considerations into account, you can objectively evaluate potential warehouse acquisitions in Baltimore. Focusing on functionality, flexibility, infrastructure condition, and operational flow will help find the ideal facility to match your business goals both today and in the future. Partnering with a knowledgeable broker and contractors during the assessment process can provide even deeper insights before making a final purchase decision.
If you’re in the market for a warehouse in Baltimore, there are several important factors to think about before signing on the dotted line. Doing thorough research ahead of time will help ensure you find the ideal space for your business’s needs, both now and in the future.
Loading Docks – Does it have enough bays for receiving inventory?
One major consideration is assessing the loading dock configuration. The number, size, type and layout of loading bays will directly impact efficiency of shipping and receiving operations. Make sure there are enough docks to handle your expected volume of deliveries and outgoing orders. Measure the dimensions of existing bays and doors to ensure they can accommodate typical trailer sizes. Look for wide aprons around the docks to allow ample room for staging and maneuvering lifts and other material handling equipment.
Also examine what direction the docks face. North-facing docks stay shaded and cooler, while southern exposure brings warmer temperatures. Positioning near main thoroughfares provides more direct access for trucks. Understanding the dock capacity and layout will inform any needs to expand or reconfigure the shipping/receiving area.
Warehouse Class – Does it meet your business needs?
Warehouse facilities are categorized into different classes based on key attributes. For example, Class A buildings are often newer construction with modern designs and systems. They offer clear ceiling heights over 28 feet, abundant power and lighting, ESFR sprinklers, and extensive loading capacity. Class B facilities may be older but functional, while Class C are more rundown “shell” spaces needing full build-outs. Make sure you choose the appropriate class to align with your budget while meeting operation requirements.
Technology – What systems are already in place?
Today’s warehouses rely heavily on technology for inventory control, order processing, automation and more. Before purchasing, assess existing warehouse management systems, barcode/RFID systems, voice technology, sensors, and equipment control systems. This will help you understand current capabilities as well as any tech upgrades needed. Also evaluate IT infrastructure such as internet connectivity speed, phone/communications, and security networks.
Power – Can it meet electricity demands?
Carefully inspect the electrical system and energy capacity. Use professionals to audit the number of panels, voltage, outlets, lighting circuits, and backup power provisions. Ensure the supply can reliably handle all sensitive electronics, charging stations, heavy equipment and machinery. Calculate expected electric loads and compare to the premises’ electrical infrastructure. Identify any upgrades needed to avoid outages or interruptions.
Location – Is it optimal for operations?
Thoroughly analyze the warehouse location relative to suppliers, logistics networks, workforce and customers. Proximity to major highways, railways, airports and ports improves efficiency. However, heavily trafficked areas also bring noise, congestion and environmental issues that could impact operations or workers. Research zoning, future development plans, and neighboring properties. The right location aligns with business distribution and labor needs.
Condition – What repairs and upgrades are required?
While fixer-uppers may seem like bargains, extensive repairs can prove costly. Inspect both the exterior and interior, looking for damage, leaks, pest infestations or signs of neglect. Assess roofing, HVAC, plumbing, electrical, sprinklers, and structural soundness. Evaluate compliance with fire, safety and accessibility codes too. Understand the true condition to budget for repairs. Enlist contractors’ help inspecting specialized building systems.
Construction – Can it accommodate inventory loads?
Review factors like building age, materials, insulation and windows that impact durability and energy efficiency. Check that the foundation and weight loading capacity can safely handle pallet racks and other inventory without compromising structural integrity. Look for robust shipping and receiving aprons that withstand heavy truck traffic. Ideally, choose economical construction that requires minimal maintenance yet delivers safety.
Layout – Does the floorplan optimize flow?
Assess how the space is currently divided into functional areas like receiving, storage, picking and shipping. Identify any bottlenecks that hinder workflow. Check aisle widths, clear heights, and accessibility to ensure efficient material transport and handling. An optimized layout enhances process flow. However, a poor existing layout may necessitate costly reconfigurations.
Parking – Is there adequate room for workers and visitors?
Evaluate parking provisions for employees, customers and truck drivers. There should be ample spaces conveniently located near entrances and docks. Review lot size, configuration and circulation patterns. Make sure large trucks and trailers can easily maneuver. If the existing parking is insufficient, look into expanding capacity onsite or leasing offsite space.
Safety – Does it prioritize worker wellbeing?
Never compromise when it comes to worker health and safety. Verify the facility has adequate fire prevention, alarms and suppression systems. Check for sufficient exits, signage and emergency lighting. Review trip and fall hazards, floor traction, racking protection, equipment guards and more. A focus on safety helps minimize risks and liabilities while improving productivity.
By taking these key factors into account, you can make an informed warehouse purchase in Baltimore that aligns with your business goals. Prioritizing functionality, flexibility, infrastructure condition and workflow will lead you to the ideal space to meet both your current and future needs. Partner with experienced contractors and advisors for deeper insights before committing.
If you’re in the market to buy a warehouse in Baltimore this year, there are many important considerations before making this major investment. Doing thorough due diligence will help you identify the ideal facility to meet your business’ needs now and into the future.
Ceiling Height – Is there enough clearance for racks and inventory?
One key factor is evaluating the interior ceiling clearance, which determines storage density and capacity. Measure not just the peak height but any beams, lights, ductwork or other potential obstructions. Consider your inventory types, storage methods and racking plans to determine ideal clearance requirements. For example, maximizing cubic storage may need modern warehouses with 32+ feet, while traditional pallet racking can function with lower heights of 24-30 feet.
Keep in mind certain building systems like ESFR fire suppression require minimum heights. Cooler/freezer spaces also often have lower ceilings. Be sure there is adequate clearance for your tallest inventory items, as well as lift equipment like order pickers. Having sufficient overhead space enables optimized usage of vertical storage real estate.
Utilities – Does it offer the right power, gas, water capacities?
Analyze whether existing electrical, gas, water/sewer and other utility service capacities can sufficiently handle warehouse operations. A thorough utility assessment is strongly recommended, considering the wide range of heavy equipment used in warehouse facilities. Look at the number of utility lines/hookups, panel amperages, outlet placements, voltage and phasing. Ensure reliable backup power provisions are in place as well.
Construction – What is the weight bearing capacity?
Review the warehouse’s construction including foundation, columns, floors, walls and roofing. Inspect the integrity to ensure the building envelope can withstand heavy racking and equipment loads over time. Check that soil compaction and foundation design accommodate anticipated live and dead loading needs. Material handling equipment and inventory introduce vibrations, so the structure must stand up to years of use. Identify any needs to reinforce the existing building shell or replace aging components.
Technology – What systems are in place?
Modern warehouse operations depend on technology integration for inventory control, order processing, shipping/receiving and more. Survey existing warehouse management systems, barcode/RFID scanning, sensors, automation, and equipment control systems. Assess gaps where technology upgrades may be beneficial as well as IT infrastructure needs.
Location – How does it optimize logistics?
Carefully analyze the warehouse location in relation to your supply chain, distribution networks and customer base. A site near major highways, railways, airports and ports improves logistics efficiency. Proximity to talented labor pools is also a plus. However, high-traffic areas can also bring congestion, noise and environmental issues that impact operations or workers. Consider zoning, future developments and neighborhood factors as well.
Parking – Is there sufficient room for workers/visitors?
Evaluate on-site parking provisions for employees, customers and truck drivers. There should be adequate spaces conveniently located near entrances and loading bays. Review parking lot size, configuration, circulation patterns and accessibility. Ensure trucks and trailers can easily maneuver. If the existing parking is insufficient, look into expanding capacity on-site or leasing off-site overflow parking.
Safety – What precautions are in place?
Warehouse safety should be a top priority to protect workers. Assess fire prevention systems including sprinklers, alarms, signage and extinguishers. Check for ample exits, emergency lighting, and back-up power. Review flooring, racking, machinery guards and equipment maintenance. Evaluate procedures and training for handling hazardous materials. A focus on safety will reduce risks and create a better workplace.
Zoning – Are there any usage restrictions?
Review zoning regulations and land use policies to ensure the warehouse property can be utilized as needed. Look into allowable uses, occupancy restrictions, and any environmental, noise or traffic mitigation requirements. Make sure there is flexibility for future expansion or facility modifications if needed. Getting zoning changes approved can be time-consuming, so understand any limitations upfront.
Taking these key warehouse considerations into account will help you objectively evaluate options and make a strategic purchase in Baltimore. Prioritizing functionality, condition, infrastructure and layout will lead you to find the perfect facility to match your business goals now and in the future. Partner with experienced advisors for deeper insights before committing.
If you’re looking to acquire a warehouse in Baltimore this year, doing thorough due diligence is key before making this major investment. Carefully evaluating critical factors will help you find the ideal facility tailored to your business’ needs.
Power – Does it have enough electrical capacity?
Assessing the electrical system and energy capacity is essential when purchasing a warehouse. The wide range of heavy machinery and sensitive equipment used in modern warehouses demands ample, reliable power. Hire electrical contractors to audit the supply voltage, panels, circuits, outlets, backup generators and overall system robustness.
Calculate your estimated electric load needs for lighting, charging stations, electronics, HVAC, machinery and other items. Compare this to the current electrical provisions to identify any shortage. Upgrading outdated panels or adding new lines and transformers may be required. Prioritize facilities with excess capacity built-in for future growth. Reliable power ensures seamless continuity of operations.
Technology – What inventory management systems are in place?
Today’s warehouses rely heavily on technology integration for tracking inventory, processing orders, shipping/receiving and more. Survey existing warehouse management systems, barcode/RFID scanning tools, sensors, automation equipment, and WiFi/cellular coverage. Determine what upgrades could boost efficiency. Evaluate IT infrastructure such as server access, speed, and cybersecurity.
Location – How does it optimize supply chain logistics?
Analyze the warehouse location respective to suppliers, distribution networks, transportation routes and customers. Sites near major highways, railways and ports improve logistics efficiency. Proximity to skilled workforces is also ideal. However, higher traffic areas also increase congestion, noise and environmental impacts. Factor in zoning, future developments and community fit.
Condition – What is the state of repair?
While fixers can be tempting, extensive repairs get costly fast. Inspect both the exterior and interior, looking for water damage, leaks, pest infestations, obsolete equipment and other issues needing remediation. Assess roofing, HVAC, plumbing, electrical, sprinklers, and structural soundness. Understand true condition to budget operating and renovation expenses accurately.
Construction – Can it support heavy inventory loading?
Review the warehouse’s construction – age, materials used, foundation, structural reinforcements, etc. Check that the building envelope, floors and roof can withstand years of heavy racking and equipment vibration without compromising stability or integrity. Identify any needs to reinforce the existing shell or replace aging components to handle maximum anticipated live and dead loads.
Layout – Does the floorplan optimize workflow?
Evaluate how the space is currently divided into functional zones like receiving, storage, picking, packing and shipping. Identify any bottlenecks or pinch points that hinder efficient workflow and material movement. Check aisle widths, clear heights and accessibility to ensure optimal product flow. A poor layout may necessitate expensive reconfigurations.
Parking – Is there sufficient room for workers/visitors?
Review on-site parking provisions for employees, customers and truck drivers. There should be adequate spaces conveniently located near entrances and loading areas. Analyze parking lot size, configuration and circulation patterns. Ensure trucks and trailers can easily maneuver. If the existing parking is insufficient, explore expanding capacity or leasing off-site overflow parking nearby.
Safety – What precautions are in place?
Thoroughly evaluate all safety provisions including fire suppression systems, alarms, exits, signage, backup lighting, equipment guarding, maintenance, and more. Review procedures for handling hazardous materials. A focus on safety helps reduce risks, protect workers, and avoid potential liabilities.
Taking these key factors into account will empower you to make a strategic, informed warehouse purchase in Baltimore. Focusing on functionality, flexibility, infrastructure condition, and layout will lead you to the ideal space tailored to your business’ needs. Partner with experienced advisors for deeper insights before committing.
If you’re considering buying a warehouse in Baltimore this year, doing thorough research is essential before making this major investment. Carefully evaluating all aspects will lead you to find the ideal facility tailored to your business’ needs.
Climate Control – Does it have heating/cooling for inventory?
Assessing climate control provisions is critical if you’ll be storing temperature-sensitive inventory. Evaluate the HVAC system capacity and zoning to maintain desired temps in office spaces versus storage areas. For food, pharmaceuticals or other climate-controlled goods, the warehouse may need chillers or separate cooler/freezer rooms.
Look at the age and condition of existing units. Check ductwork, insulation, seals and filters. Consider seasonal impacts on HVAC load. Upgrading outdated systems may be required to efficiently regulate multi-zone or specialized temperature requirements. Proper climate control protects inventory from damage and spoilage.
Fiber Optics – Does it have high speed data capacity?
Modern operations rely on lightning fast data exchange. Evaluate existing fiber optic infrastructure for sufficient speed and reliability. This includes broadband networks, CAT6 wiring and WiFi coverage throughout the facility. Look for extra capacity to support inventory management systems, order processing, security feeds and equipment controls.
Zoning – Are there any usage restrictions?
Review zoning regulations to ensure the property can be used as needed. Check permitted uses, occupancy limits, environmental impact rules, and other municipal codes. Make sure there is flexibility for future expansion or facility modifications. Navigating zoning changes can be time-consuming. Understanding any existing limitations is critical.
Exterior – How durable and secure is the envelope?
Assess the exterior construction including walls, entrances, windows and roofing. Look for durable materials that withstand weather and boost energy efficiency. Make sure exterior lighting deters crime while respecting neighbors. Consider fencing, gates, traffic patterns and landscaping. A secure site protects your assets.
Sprinklers – Does it have adequate fire suppression?
Evaluate the warehouse fire sprinkler system to ensure sufficient coverage for inventory protection. This may include ESFR sprinklers to suppress high-challenge fires up to 30 feet. Make sure the water supply and piping can provide needed volume and pressure. Additionally, assess fire alarms, signage, exits and other life safety systems.
Staff Facilities – Are amenities adequate?
While focused on operations, don’t overlook employee considerations. Evaluate existing office, locker room, breakroom and bathroom accommodations. If lacking, budget upgrades like added bathrooms, larger break areas and enhanced parking. Providing proper amenities improves recruitment, retention and productivity.
Hazmat Storage – Can it safely contain chemicals?
If handling hazardous materials, ensure the facility can properly store and segregate risky inventory. This may involve leakproof containers, explosion-proof fixtures, spill containment systems and specialized ventilation. Review protocols and permitting requirements for hazmat handling. Don’t take chances when it comes to environmental and personnel safety.
Taking all of these factors into careful consideration will enable you to make a strategic, informed warehouse purchase in Baltimore. Prioritizing functionality, safety, infrastructure condition and layout will lead you to the perfect space meeting your business’ needs, both for today and future growth. Partner with experienced advisors for deeper insights before committing.
If you’re exploring buying a warehouse in Baltimore this year, conducting comprehensive due diligence is critical before committing. Carefully assessing all aspects will empower you to find the ideal space meeting your business’ needs.
Security – What security features does it have? Alarm, cameras?
Assessing security provisions should be a top priority when selecting a warehouse facility. Review features such as perimeter fencing, gates, exterior lighting, alarm systems, and video surveillance coverage. Look at how exterior doors, windows, roof hatches are secured. Consider 24/7 monitoring and patrols if in a higher-crime area.
EvaluateRestricted access controls, visitor procedures, and internal security protocols also limit vulnerabilities. Ensure robust cybersecurity for inventory management systems and data exchanges. Don’t underestimate security – it protects your assets, maintains trust with clients, and prevents inventory shrinkage.
Accessibility – How convenient is it for workers/trucks?
Analyze the warehouse’s location and accessibility relative to main roads, highways, interstates and transportation hubs. Convenient access minimizes commute times for employees and speeds freight journeys. However, highly-trafficked areas also bring congestion, noise and environmental impacts to consider. Close proximity to suppliers and customers is ideal.
Office Space – Is there room for administrative functions?
Evaluate existing office build-outs and meeting rooms. For many operations, ample office space is key for carrying out administrative tasks in a comfortable environment separate from the production floor. If the available office space is insufficient or outdated, factor in costs to expand build-outs.
Loading Configuration – Does it support needed throughput?
Carefully assess the loading dock configuration including number of doors, door dimensions, levelers, seals, bumpers and apron space. Docks should facilitate efficient material movement in and out of the facility. Verify docks are positioned conveniently for routing trucks. Lacking appropriate docks will hamper your shipping and receiving activities.
Maintenance – What equipment/systems need upgrading?
Inspect facility infrastructure – HVAC, electrical, plumbing, roofing, etc. and identify any aging components due for replacement. Check for leaks, broken hardware, pest infestations or other issues requiring immediate repair. Develop a maintenance budget accounting for near-term upgrades as well as future capital projects. Proper maintenance optimizes building lifespan.
Flow – Does the layout optimize efficient operations?
Evaluate how the space is divided into functional areas like receiving, storage, picking and shipping. Identify any constraints that create bottlenecks or hinder material movement. Analyze openness, aisle widths, clearance heights that impact accessibility and maneuvering. An optimized layout enhances workflow.
Expansion – Is there room to grow onsite?
Consider not just your current space needs, but future growth requirements as well. Look for vacant land or other buildings onsite to allow scaling up operations down the road without relocation. If expansion potential is limited, factor in the possibility of having to move entirely to meet long-term business growth.
Taking all of these important factors into account will enable you to objectively evaluate options and make the best warehouse purchase in Baltimore for your company. Partner with experienced contractors and advisors for deeper insights before finalizing a deal.
If you’re exploring buying a warehouse facility in Baltimore this year, doing thorough due diligence is key before making this major investment. Carefully evaluating all aspects will lead you to find the ideal space meeting your needs.
Price – What is your budget? How does it compare to other listings?
When analyzing potential warehouses, price should be considered in conjunction with factors like size, condition, location and capabilities. Determine your budget for purchase price or lease terms, factoring in needed renovations, equipment and operational costs. Require the seller to provide clear cost breakdowns.
Compare listing prices to assess fair market value. Look at the price per square foot or monthly net rent. Weigh costs against the functionality and features being offered. Don’t assume lower priced fixers are bargains once renovation bills are factored in. Understanding true costs informs negotiating leverage and avoidance of overpayment.
Lighting – Does it provide optimal visibility?
Assess lighting provisions for adequate illumination of work areas without excessive glare or shadows. Look for modern LED fixtures paired with smart controls and sensors to maximize efficiency. Emergency backup lighting should also be evaluated. Proper lighting benefits productivity, accuracy, safety and energy savings.
Signage – Is there clear directional/safety signage?
Interior signage provides visual communication for safe, efficient operations. Confirm adequate wayfinding, safety warnings, area designations and informational signs. Compliant building signage directs emergency responders. Exterior signage gives direction. Ensure signs are visible, unambiguous and placed appropriately.
IT Infrastructure – Does it support inventory systems?
Modern warehouses rely on robust IT frameworks to power inventory control, order processing and other systems. Assess existing servers, network equipment, fiber optic wiring, wi-fi coverage and cellular reception. Identify gaps needing upgrades for speed, capacity and redundancy. Factor in costs for technology improvements.
Insurance – How much coverage is recommended?
Consult with insurance advisors when evaluating facilities to understand recommended coverages and potential savings from safety features. Look for additions like theft protection, flood insurance, earthquake policies, umbrella liability coverage and more based on risk profile. Adequate insurance mitigates unforeseen costs.
Compliance – Does it meet codes and regulations?
Carefully assess facility compliance with zoning, fire/life safety, accessibility, environmental and other municipal codes. Evaluate emergency systems, hazardous storage, stormwater provisions and more against regulations. Ensure there are no major violations requiring remediation. Non-compliance risks fines, shutdowns and liability.
Weighing all of these factors will empower you to make a strategic, informed warehouse purchase in Baltimore. Conducting due diligence saves money and avoids headaches. Partner with experienced advisors to evaluate all considerations before finalizing a deal.
If you’re exploring purchasing a warehouse facility in Baltimore this year, conducting comprehensive due diligence is essential before committing. Thoroughly evaluating all aspects will lead you to the ideal space meeting your needs.
Financing – Will you need a business loan or commercial mortgage?
Before searching for warehouses, get financing pre-approved to understand your true price range and loan terms. Seek quotes from lenders on commercial mortgages, SBA loans, equipment leasing and lines of credit. Compare interest rates, fees, loan amounts and collateral required.
Evaluate the impact of different down payment amounts on your monthly payments. Understand loan amortization schedules and balloon payments if applicable. Make sure financing aligns with business cash flow projections. Having financing pre-arranged makes negotiations easier and avoids disappointments.
Natural Light – Does it maximize daylighting?
Assess window placement and skylights to understand how much natural light permeates work areas. Proper daylighting boosts productivity, morale and safety while reducing energy costs. Just be sure glare and heat gain are controlled. If existing light is insufficient, consider solatubes, window films and light shelves to improve ambient brightness.
Stormwater Management – Does it meet drainage requirements?
Review the property’s stormwater provisions including drainage channels, catch basins, and retention ponds. Check permits and compliance with stormwater management regulations. Make sure runoff is properly diverted from structures and contained onsite without impacting operations or neighbors.
Roof – What is its condition and lifespan?
Inspect the roof age, material, drainage and penetrations. Check for leaks, damage, ponding and deterioration. Understand remaining lifespan and warranty details. Budget for any replacement or repair costs in the near future. Proper roofing is essential for weatherproofing, insulation and safety.
Loading Configuration – Does it support needed throughput?
Carefully assess the loading dock configuration including number of doors, door dimensions, levelers, seals, bumpers and apron space. Docks should facilitate efficient freight movement in/out of the facility. Verify docks are positioned conveniently for routing trucks. Insufficient docks will hamper shipping/receiving activities.
Taking all of these important factors into account will enable you to make the best warehouse purchase in Baltimore for your company. Partner with experienced contractors and advisors for deeper insights before finalizing a deal.
If you’re exploring purchasing a warehouse facility in Baltimore this year, conducting comprehensive due diligence is critical before making this major investment. Thoroughly evaluating all aspects will lead you to find the ideal space meeting your needs.
Inspections – Were thorough building and environmental inspections done?
Before committing to a warehouse, insist on detailed inspections by qualified professionals. A rigorous evaluation of structural, mechanical, electrical, roofing and other systems identifies any deficiencies needing repair. Environmental assessments uncover risks like soil contamination.
Structural inspections verify sound foundation and load-bearing elements. Roof inspections look for leaks, age, drainage issues and material failures. Mechanical inspections review HVAC equipment, plumbing, fire suppression systems and more. Electrical inspections confirm sufficient power supply and code compliance. Hire appropriate experts to provide comprehensive condition assessments.
Location – How does it optimize supply chain logistics?
Analyze the warehouse location respective to suppliers, distribution networks, transportation routes and customers. Sites near major highways, railways and ports improve logistics efficiency. Proximity to talented labor pools is also ideal. However, higher traffic areas also increase congestion, noise and environmental issues that impact operations or workers. Consider zoning, future developments and community fit.
IT Infrastructure – Does it support inventory systems?
Modern warehouses rely on robust IT frameworks to power inventory control, order processing and other systems. Assess existing servers, network equipment, fiber optic wiring, wi-fi coverage and cellular reception. Identify gaps needing upgrades for speed, capacity and redundancy. Factor in costs for technology improvements.
Loading Configuration – Does it support needed throughput?
Carefully assess the loading dock configuration including number of doors, door dimensions, levelers, seals, bumpers and apron space. Docks should facilitate efficient freight movement in/out of the facility. Verify docks are positioned conveniently for routing trucks. Insufficient docks will hamper shipping/receiving activities.
Safety – Does it meet codes and offer hazard protections?
Evaluate all safety provisions including fire systems, exit signs, hazmat storage, equipment guarding, accident prevention procedures and more. Look for adequate zoning of fire risks and containment of dangerous inventory. Make sure training and compliance programs are in place to mitigate hazards and risks.
Taking these key warehouse factors into careful consideration will lead you to make a strategic, informed purchase in Baltimore. Conducting thorough due diligence protects your investment and avoids costly surprises down the road. Partner with experienced advisors during the evaluation process for deeper insights before committing.
If you’re exploring buying a warehouse facility in Baltimore this year, conducting thorough due diligence is critical before committing. Carefully evaluating all aspects will lead you to the ideal space meeting your needs.
Negotiation – Is the seller flexible on price or terms?
Before entering negotiations, know your “walk away” threshold based on due diligence findings. Consider creative terms like seller financing or lease-to-own options to bridge gaps if needed. Consult brokers to benchmark fair asking prices for turn-key modern warehouses in the target area on a price per square foot basis.
Get multiple repair estimates to quantify renovation costs. Use this to negotiate credits or price reductions for identified deficiencies. Negotiate closing contingencies like inspections and financing to avoid being stuck with a deficient property. Work collaboratively to find a win-win agreement that provides you a functional facility at a justifiable price.
Office Space – Is there room for administrative functions?
Evaluate existing office build-outs and meeting rooms. For many operations, ample office space is key for carrying out administrative tasks in a comfortable environment separate from the production floor. If the available office space is insufficient or outdated, factor in costs to expand build-outs.
Maintenance – What equipment/systems need upgrading?
Inspect facility infrastructure – HVAC, electrical, plumbing, roofing, etc. and identify any aging components due for replacement. Check for leaks, broken hardware, pest infestations or other issues requiring immediate repair. Develop a maintenance budget accounting for near-term upgrades as well as future capital projects. Proper maintenance optimizes building lifespan.
Lighting – Does it provide optimal visibility?
Assess lighting provisions for adequate illumination of work areas without excessive glare or shadows. Look for modern LED fixtures paired with smart controls and sensors to maximize efficiency. Emergency backup lighting should also be evaluated. Proper lighting benefits productivity, accuracy, safety and energy savings.
Safety – Does it meet codes and offer hazard protections?
Evaluate all safety provisions including fire systems, exit signs, hazmat storage, equipment guarding, accident prevention procedures and more. Look for adequate zoning of fire risks and containment of dangerous inventory. Make sure training and compliance programs are in place to mitigate hazards and risks.
Taking all of these important factors into account will empower you to make the best warehouse purchase in Baltimore for your company. Partner with experienced advisors to guide negotiations and due diligence.